In the fill-finish manufacturing of parenteral liquid pharmaceuticals, maintaining product sterility is paramount. The choice of what kind of barrier technology to utilize becomes key, as operations must account for the production environment and the level of control and efficiency needed to hit key production milestones. For an increasing amount of industry professionals, isolators are becoming the preferred choice, a reality reflected by the latest Annex 1’s heightened emphasis on Isolator-related operations. The level of control, automation, and precision offered by high-quality isolator solutions continue to demonstrate clear advantages for the drug development process, particularly as the market continues to be shaped by the growing utilization of patient-centered medicine.
In any given isolator design, implementing a robust airflow strategy to maintain a Grade A space is critical. Maintaining First Air – filtered unidirectional air that has not been interrupted prior to contacting exposed product and product contact surfaces for particulate-free aseptic processing- is the primary goal of airflow design, as laminar airflow is a sterile product’s last defense against contamination. In our new isolator,designed and manufactured in collaboration with Germfree, AST wanted to present a best-in-class airflow solution that embodied the latest advancements and provided innovative solutions for common issues and pain points encountered in fill-finish isolator operation.
Wherever the Wind Blows: Assessing Air Handling Obstacles
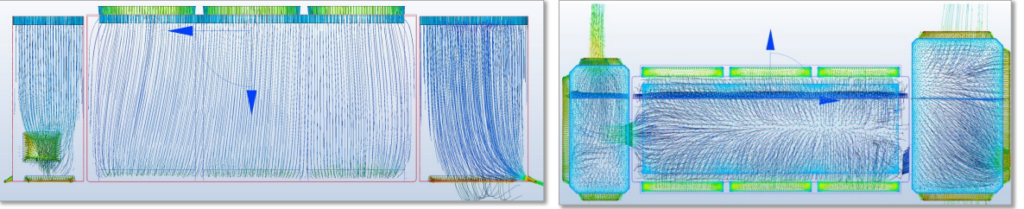
Every isolator design must navigate specific air-handling obstacles in order to be functional and effective. Beyond adhering to industry standards (aspects like HEPA filter coverage and proper airflow velocity), how one anticipates and resolves design limitations, as well as the operating parameters of the specific machine housed inside the isolator, is key. Issues like dead zones where fully circulated air may fail to reach, structural obstructions of the filters, air diffuser membrane placement, and pressure differences between modules that can cause air vortices that work against the unidirectional airflow are all obstacles that can be mitigated with a quality-by-design approach. And in cases of troubleshooting air-related issues, what’s the best approach? Should it, for example, take hours of searching to find an air leak that’s causing a failed pressure decay test?
In the collaboration process with Germfree on the design of our isolator, both teams were able to come together with their collective expertise and years of experience in Grade A air solutions. The process started with the AST team running computational fluid dynamics analysis (CFD) on airflow to inform the design and build configurations of the isolator. This allowed the team to anticipate and resolve simulated air flow issues and to test different variations of the design. They were able to isolate probable dead zones, identify and resolve pressure drops and airflow vortexes (Figure 2.), assess different variations of filter placement, and dial in the design until it reached the exact readings ideal for aseptic fill-finish processing (Figure 1).
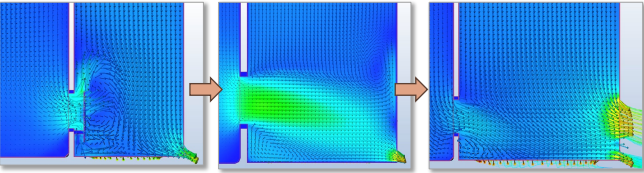
An Isolator Designed for Optimal Airflow
Once the design was perfected through CFD simulations, we began the process of turning a concept into reality. The AST isolator has specific features designed to promote and sustain consistent unidirectional air flow throughout the entire isolator, including:
- Wide open chambers in every module for minimal airflow disturbance
- Precise placement between HEPA filters and air distribution membrane, allowing membrane to eliminate all possible stagnant airflow pockets and avoiding any structural obstructions
- Intake and exhaust plenums are completely separate for efficient air exchanges; Programmable for 100% exhaust or recirculation
- An integrated PAO generator for efficient filter integrity testing
- A closed loop, positive pressure system, including automated decontamination measures that introduce no outside air into the isolator
- Comprehensive sensor coverage that monitors the conditions of the isolator at all times and immediately alerts the operator of an issue, including precise leak detection
Grade A Air Bolstered by Aseptic Robotic Technique
The final piece of the airflow puzzle is the quality of the fill-finish system in the hands of a trained operator. The choice of aseptic processing system should play a key role in the operator’s sterility strategy as a fill line and isolator should fit hand in (validated) glove. An approach that considers the entire operation and prioritizes the seamless integration between an isolator and the aseptic processing systems establishes a holistic, sustainable fill-finish solution. It’s important to have high-quality, effective barrier technology; however, the benefits can quickly be diluted by sub-optimal fill-finish systems. This is especially true when it comes to air handling. Just as there is proper aseptic technique for gloved interventions to ensure that First Air is maintained, advanced robotic operations should be designed for minimal disturbance of laminar air flow over exposed product. The AST isolator is designed with the same philosophy and precision that engineered our aseptic processing solutions: We have tested and implemented automated robotic methods that maintain First Air in the most advanced, sensitive fill-finish operations, offering operators unparalleled functional flexibility like processing directly in the nest. Having fully integrated, turnkey barrier and fill-finish technology provides the foundation for consistently achieving the highest level of product integrity and viability. Learn how AST can provide your organization with the next generation of high-quality isolator technology – contact our experts today.