When determining your approach to building an aseptic processing line, one of the first choices customers face is between custom builds to meet product specifications versus the use of modular, configurable technology. Whether you’re relatively new to the aseptic fill-finish process or a seasoned industry professional, the evolving nature of sterile parenteral products and their accompanying technologies and regulations can be daunting. The manufacturing solutions available vary a great deal by the stage of development (drug discovery all the way up through commercial production), product demands (high yield and targeted production vs bulk, high output production), mode of operation (manual, semi-automated, fully automated), and number of products and formats (static lines vs multi-modal, flexible systems) to name a few. A knowledgeable aseptic processing partner will be able to help you navigate through these important factors and find the solutions that best meet your operational needs.
While custom fill-finish solutions may be appropriate for select, highly specialized products, the rise of modular, configurable technology has opened up new possibilities for the pharmaceutical market in general and patient-centered medicine in particular. Why has this been the case? The answer lies in three key performance attributes for any pharmaceutical manufacturer: cost, time and reliability.
A comprehensive approach to modular configuration addresses these areas with advanced, intuitive designs. Predesigned, prefabricated models significantly reduce lead time and enable accurate project scheduling and estimation, which is critical when planning operational milestones and implementing time-to-market strategies. Modular configurations also significantly lower the cost of a machine, requiring fewer overall engineering hours that would otherwise go to the custom design and build of the line—a significant front-end investment. Additionally, custom solutions can come with substantial amounts of troubleshooting and scope adjustments depending on obstacles or new insights that appear as the project matures.
Custom fill lines can also feature first-of-its-kind technology which can be unpredictable and are untested in real-world manufacturing situations. At the heart of the choice between a customized and configurable approach is the level of uncertainty that an operation is comfortable with. The initial performance of the equipment, along with lifecycle variables like maintenance intervals, durability, and parameters of stock/aftermarket support, are all yet to be determined with custom, first-generation technology. Additionally, from a regulatory and operational framework, new technology means new documentation, new testing protocols and new training materials, all of which are absolutely necessary to a pharmaceutical operation. Here, having well-designed, highly repeatable, and predictable technology is a demonstrable advantage.
AST’s Configurable Modular Technology: Tailored and Proven
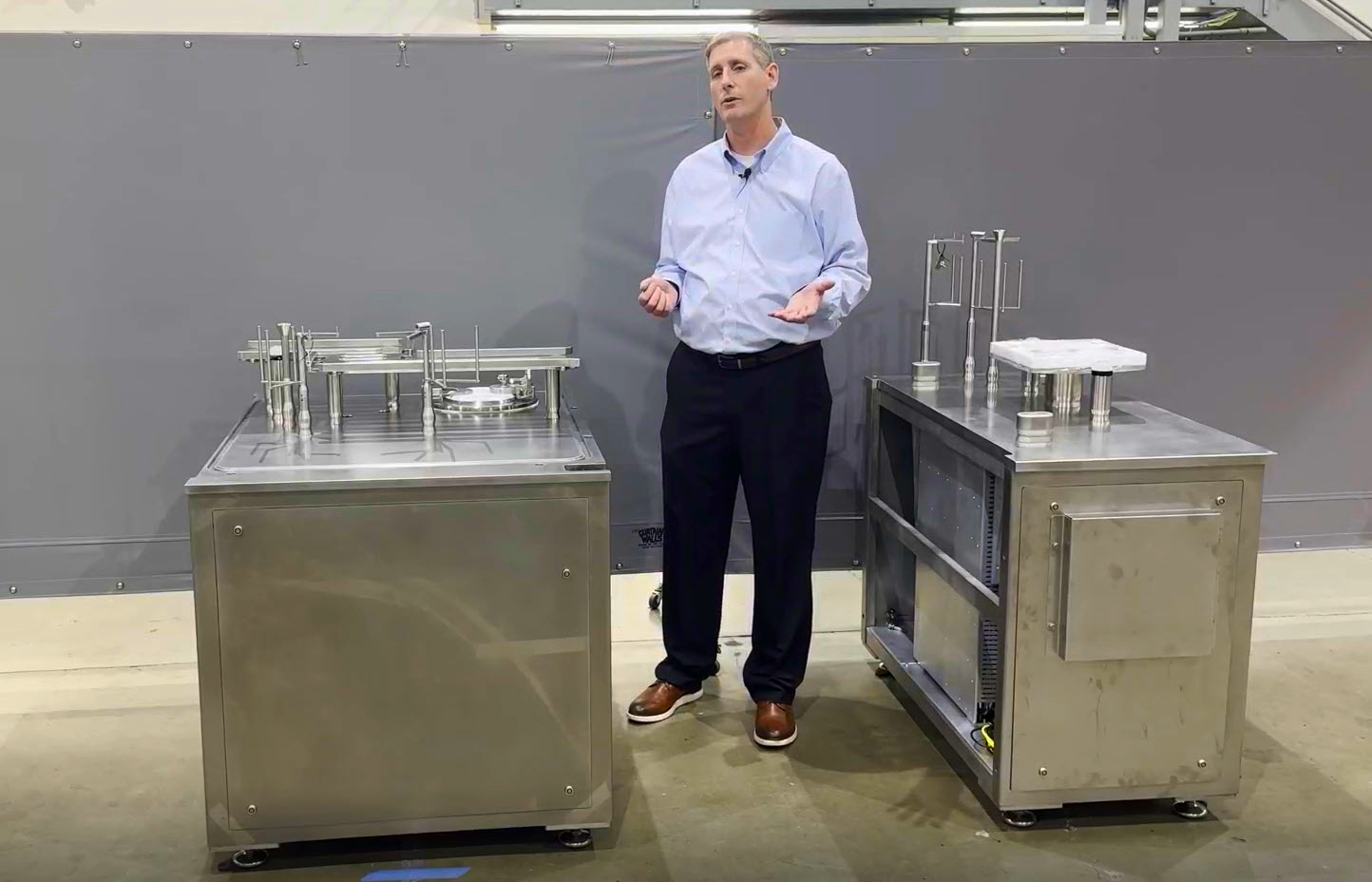
Josh Russell demonstrating AST’s approach to configuration with the Semi-Automatic Bag Opener (SABO) and Manual Tub Opener (MTO) modules at the 2024 Virtual Pharma Expo.
Configurable modular fill-finish lines consistently perform in four key areas:
Quality: A modular design means that the quality and engineering behind any given technology has been rigorously evaluated, reworked, refined, and goes through an ongoing cycle of continuous improvement. New innovations and improvements in materials and engineering technology will continue to inform a module with each new iteration. AST’s modular technology is the net result of the best practices and best craftsmanship available.
Dependability: Solutions featured in a configurable line are tested, proven technologies, which means they have a proven track record of validation, durability, and use logic rooted in real-time manufacturing parameters. They’re also backed by data-informed maintenance schedules, troubleshooting services, and spare part & consumables forecasting.
Performance – An aseptic processing operation is a significant investment of time and resources, so the performance of the chosen equipment is paramount. That’s why being able to configure a fill-finish line to the specific demands of a drug product, especially for high-value liquid pharmaceuticals that require no waste and high-yield strategies, has changed the way the industry approaches pharmaceutical manufacturing. Modular configuration, when combined with single-use and ready-to-use technology, provides an avenue for manufacturers to leverage solutions that have a proven history of results with a zero-waste approach from the very start of production. That means complete product stewardship from the very first container that is run through the machine.
Flexibility: The strength of a configurable approach is in its adaptability. Configuration isn’t static; it’s about having the right building blocks available—an extensive inventory of aseptic processing technologies able to meet the majority of process conditions required by the full range of parenteral drug products. Whether it’s adjusting or upgrading a modular block or adding a module in to fit a new process, the modular approach is one that is intended to fit and scale with your operation.
Learn how AST can help your organization find the ideal aseptic processing approach with our next-generation fill-finish technologies – contact our experts today.