PRODUCTS
The ASEPTiCell: The Full Power of Robotics in One Flexible Production System
The ASEPTiCell® is where the full power of AST’s automated and robotic solutions meet precision modular engineering for the commercial production of medium-batch liquid pharmaceuticals. Fully automated from start to finish, this highly intuitive, flexible fill-finish system was the industry’s first aseptic multi-format processing machine capable of processing ready-to-use nested vials, cartridges, and syringes on the same line. The latest-generation ASEPTiCell builds on that initial innovation, offering industry-leading multi-modal flexibility, efficiency with recipe-driven production, and fewer change parts for minimal format changeover time and optimal machine uptime.
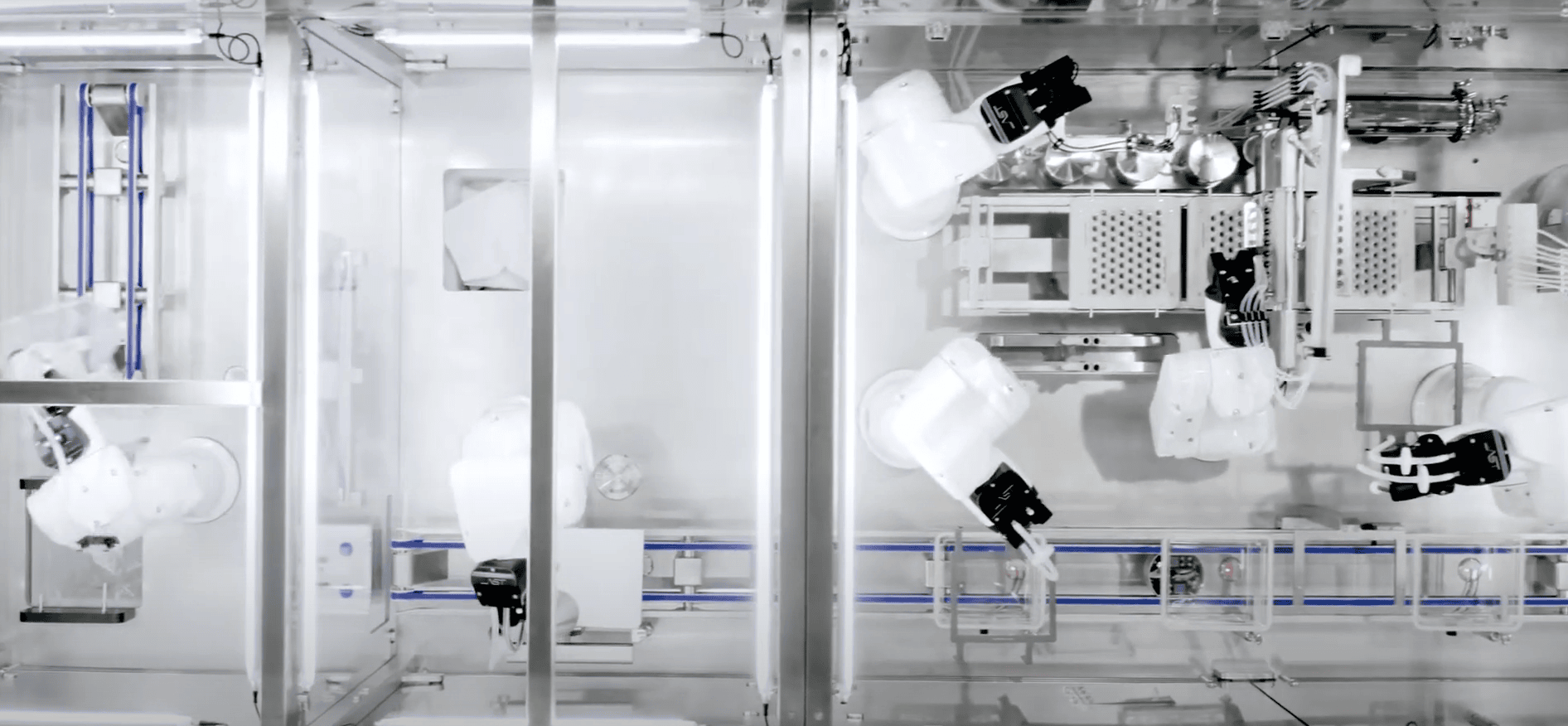
In the Know
Capabilities
- Tested, standardized modules configurable for fully automated commercial processing needs
- cGMP technology across all modules
- Universal RTU container processing capabilities
- Scalable solutions for easy validation and efficient technology transfer
- Product stewardship measures for quality control and high-value products
- Full ramp-up support, including qualification services and full documentation packages
- Responsive, 24/7 aftermarket support throughout the life of your equipment
- Isolator or RABS configuration
- Compact, Integrated configuration for a smaller operational footprint
- Processes up to 100 units per minute
- Configurable, recipe-driven production
- Toolless change parts
- Processing tools and robotics never drop below working height
- Processes vials, syringes, and cartridges on the same line with minimal changeover time between formats
- EM suite design, including optional automated plate handling
- No glass-on-glass or glass-on-metal contact eliminates common quality challenges
- Peristaltic and rotary piston pump options
- ASTView, a centralized HMI for intuitive operation and data retention, and an optional EBR system for 21 CFR Part 11 Compliance
- For syringes and cartridges, Piston insertion for options for the full scope of drug product properties and sensitivities
The ASEPTiCell is the ideal solution for parenteral drug manufacturers looking for a higher throughput and larger batch-size processing. The system features a throughput of one hundred units per minute and can process batch sizes of 30,000 units or higher. For vial processing, the latest generation system comes with AST’s new VSM-100 for high-speed vial capping. Additionally, the system is available with 100 percent IPC functionality with no compromise to machine output.
When combined with the new Atmos™ isolator, The ASEPTiCell is a robust fill-finish system with industry-leading cycle times (1 hour, including aeration) and designed as a comprehensive, user-friendly turnkey solution.
The ASEPTiCell leverages the latest in robotics and automation for the flexible processing of RTU Containers. This is advantages of end end-to-end robotic include:
- Build for ISO 5 – Grade A operations
- Non-absorptive & microbially resistant
- FDA compliant
- VPHP compatible
- Minimal human interventions
- Intuitive design, made for round-the-clock operation
- Gentle container handling
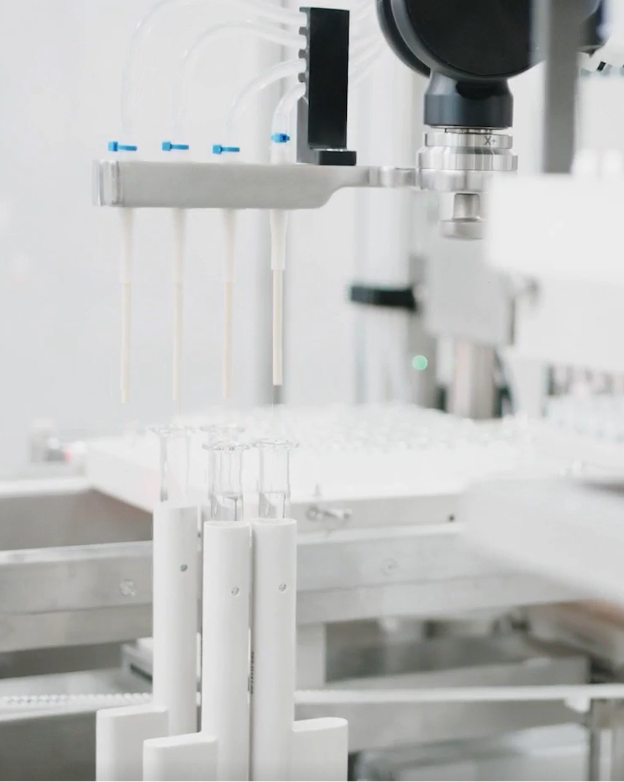
Interactive Diagram of ASEPTiCell | Click a Hotspot
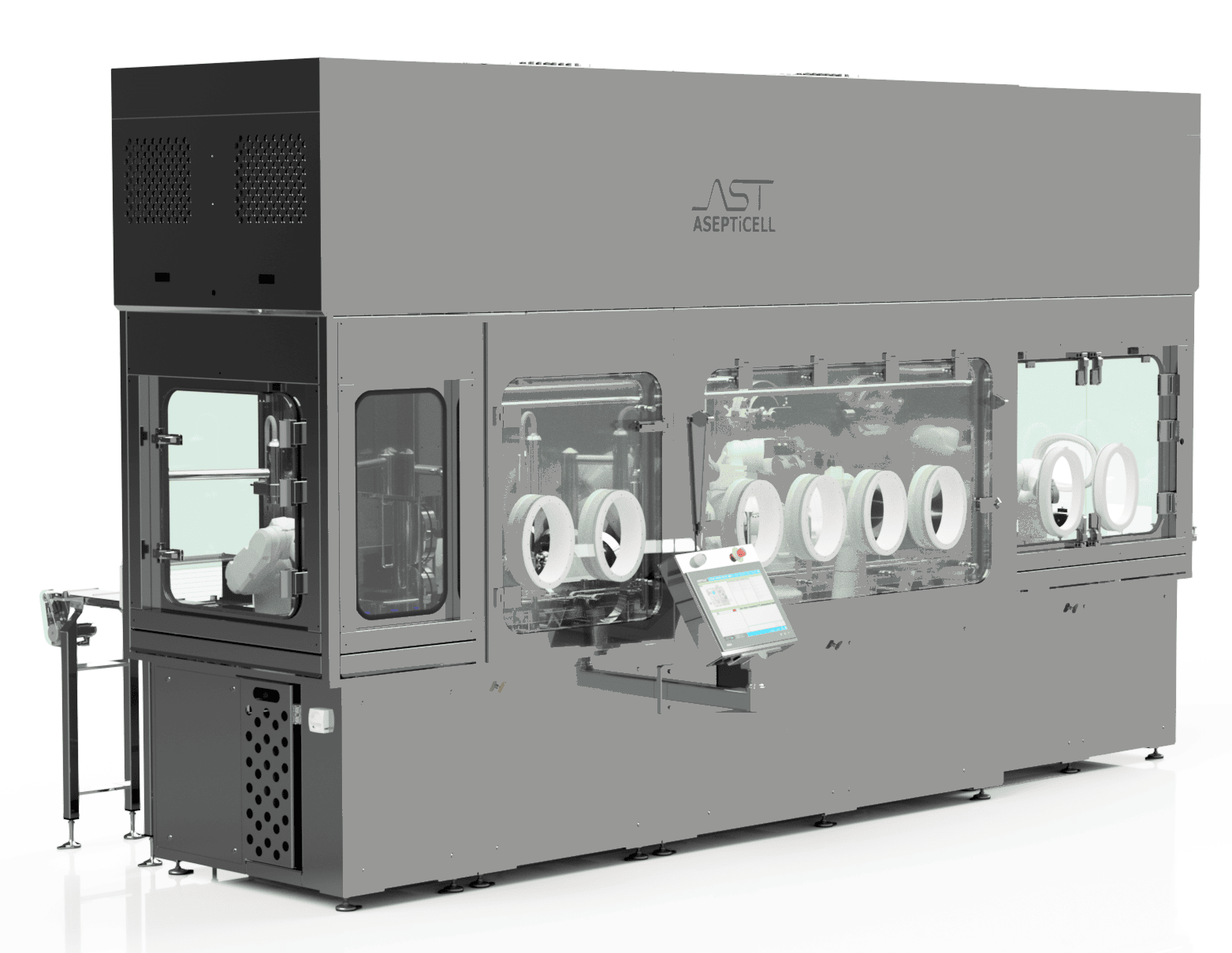
Automatic Bag Opening with hygienic trash removal and no-touch transfer into Grade A space
Robotic tub handling with seal removal and staging with minimal particle generation
ASTView, a centralized HMI fully integrated fill-fish and barrier system operation and data retention
Robotic, recipe-driven filling and closing of containers with in-line quality controls, product recovery and reject handling
Annex 1 Compliant High Speed Vial Capping
Atmos™ Isolator Technology for Grade A air handling and critical zone processing
The Next Tier of No-Touch Technology
Lead time and machine changeover requirements are crucial to the time-to-market equation for pharmaceutical manufacturers. The built-in philosophy at AST approaches fill-line configurations in an adaptable way that prioritizes customer’s specifications. Like grabbing the right tools from a toolbox, AST’s modular approach enables our team to capture the majority of requirements with our existing modular solutions, which allows very rapid configuration, delivery, validation, and launch of an operation.
The available modules on the ASEPTiCell are:
- ABO – Automatic Bag Opening
- ATO – Automatic Tub Opening
- FCM – Fill / Close Module
- LPM/LTM – The Lyo Processing and transfer module
- VSM – Vial Sealing Module (also available in a linear configuration)
- OFM – Outfeed module
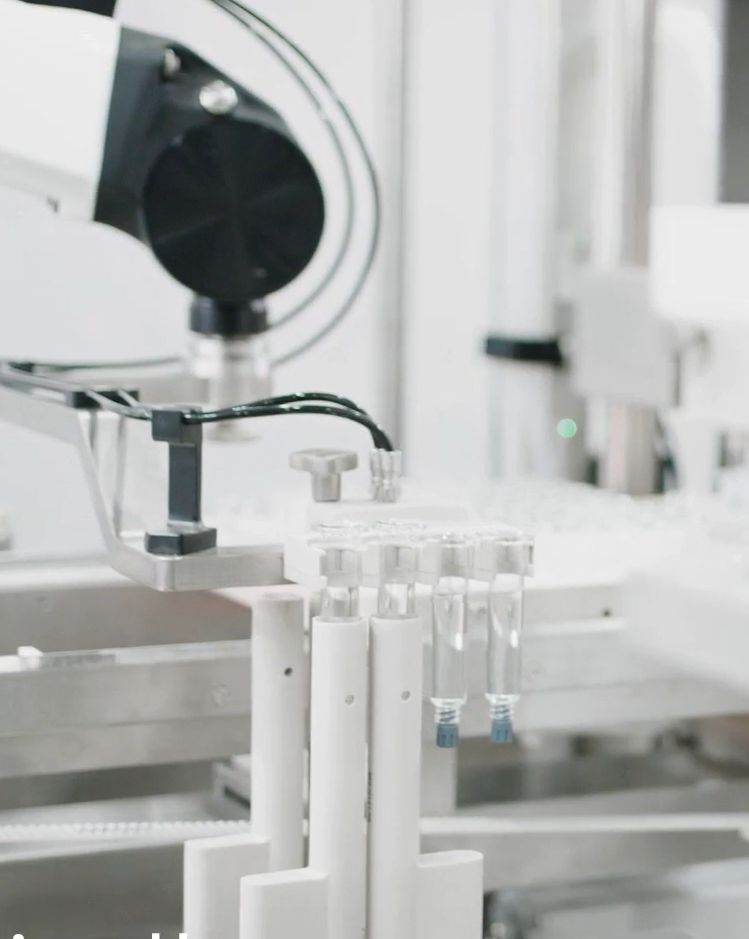
You've seen the ASEPTiCell in motion...
Perhaps it's time to discover how it would work with your application?
Meeting Industry Needs | Applications
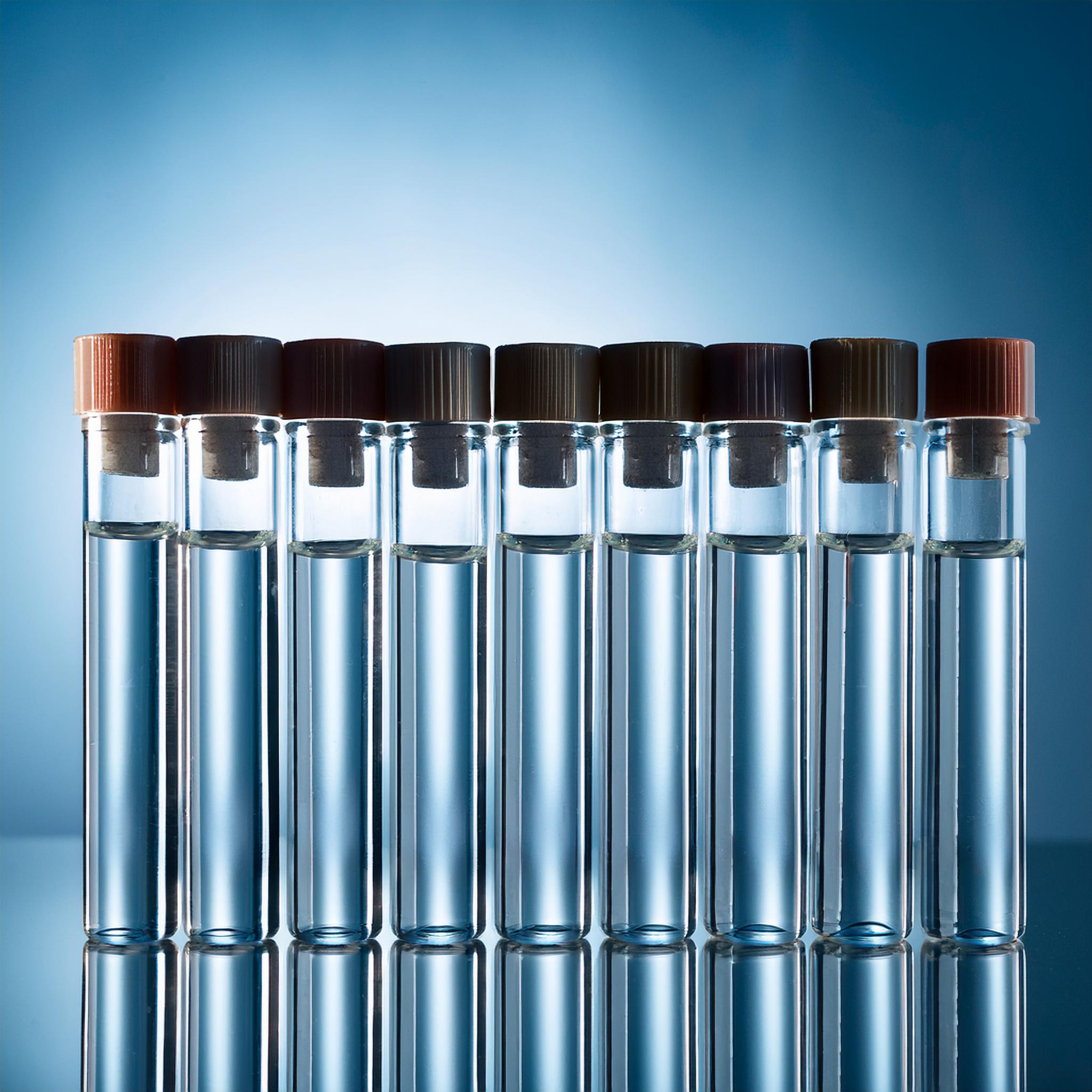
AST has led the flexible aseptic manufacturing movement since the design and launch of our first ASEPTiCell, which was the industry’s first multi-format system designed to process ready-to-use nested vials, cartridges and syringes. Now an industry standard, multi-modal pharmaceutical manufacturing stakeholders are looking for ways to grow pipeline agility through proven cGMP technology. AST’s ASEPTiCell offers fill-finish processing for the full range of commercial and custom RTU formats and product applications.
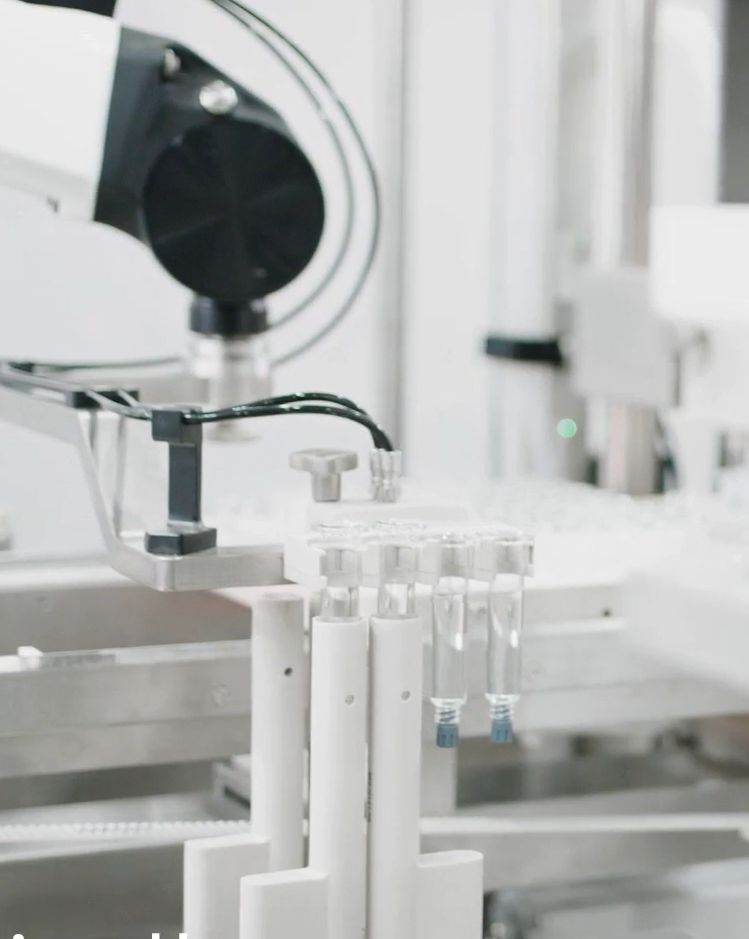
AST’s robotics are designed to execute critical processes with precision and repeatability across the fill-finish line. Simplified, well-designed movements are a way to ensure that robotic handling adheres to proper aseptic technique, which is especially crucial in critical zones and for cGMP compliance, including alignment with the new Annex 1. Robotic processing in the ASEPTiCell minimizes air disturbance over exposed product, and unidirectional airflow is always maintained.
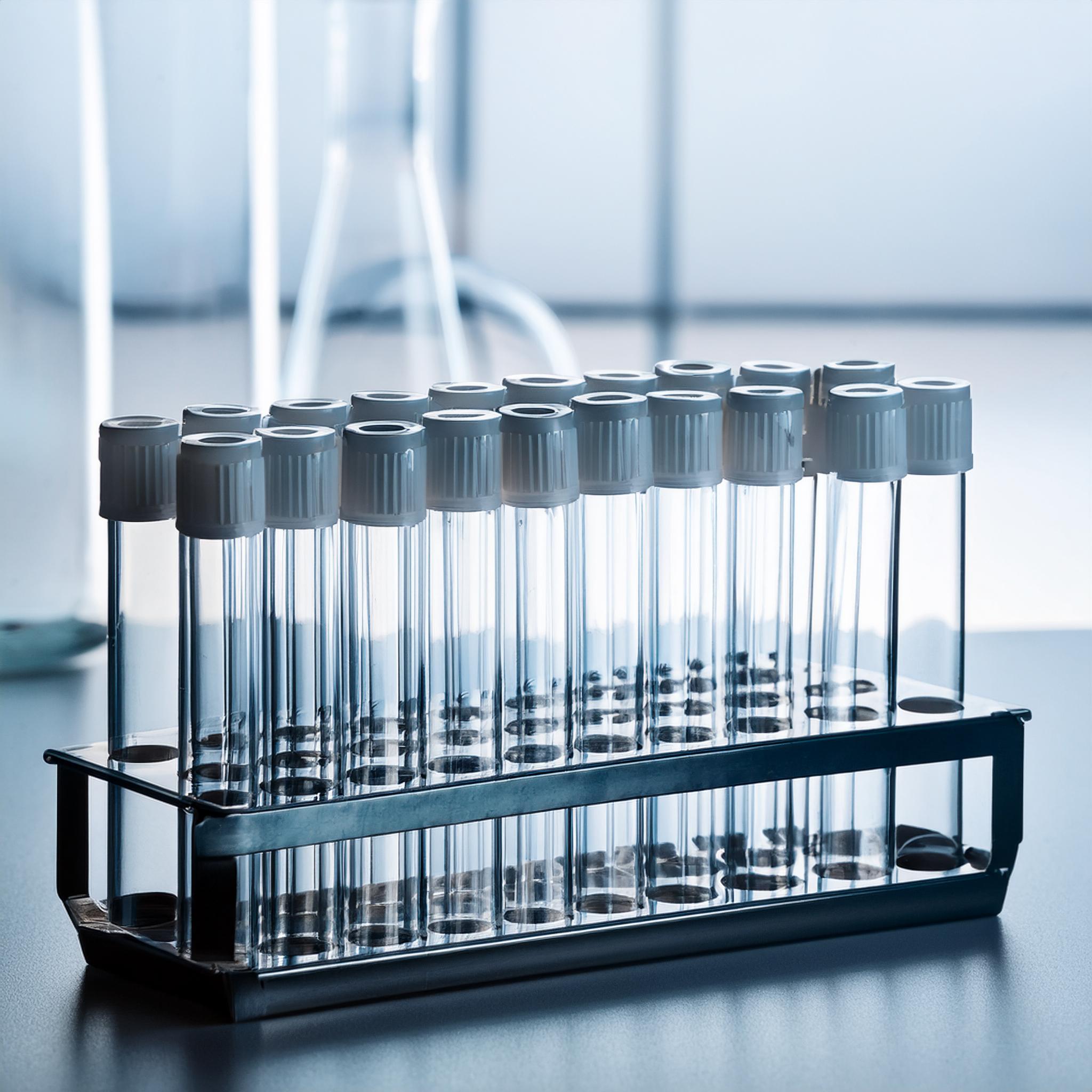
When compared to other similar solutions, the ASEPTiCell offers a more compact, flexible solution with the same optimization for throughput and quality. Designed as a 100 percent integrated solution that leverages latest is hygienic robotic technology in a powerful turnkey system that features end-to-end flexibility, product stewardship, and programmable, recipe-driven operations. Important operations features including hands-free de-packaging and container handling, automated visual inspections, in-process weight checks, and fast format changeover of robotic tooling for processing vials, cartridges, and syringes on the same line.
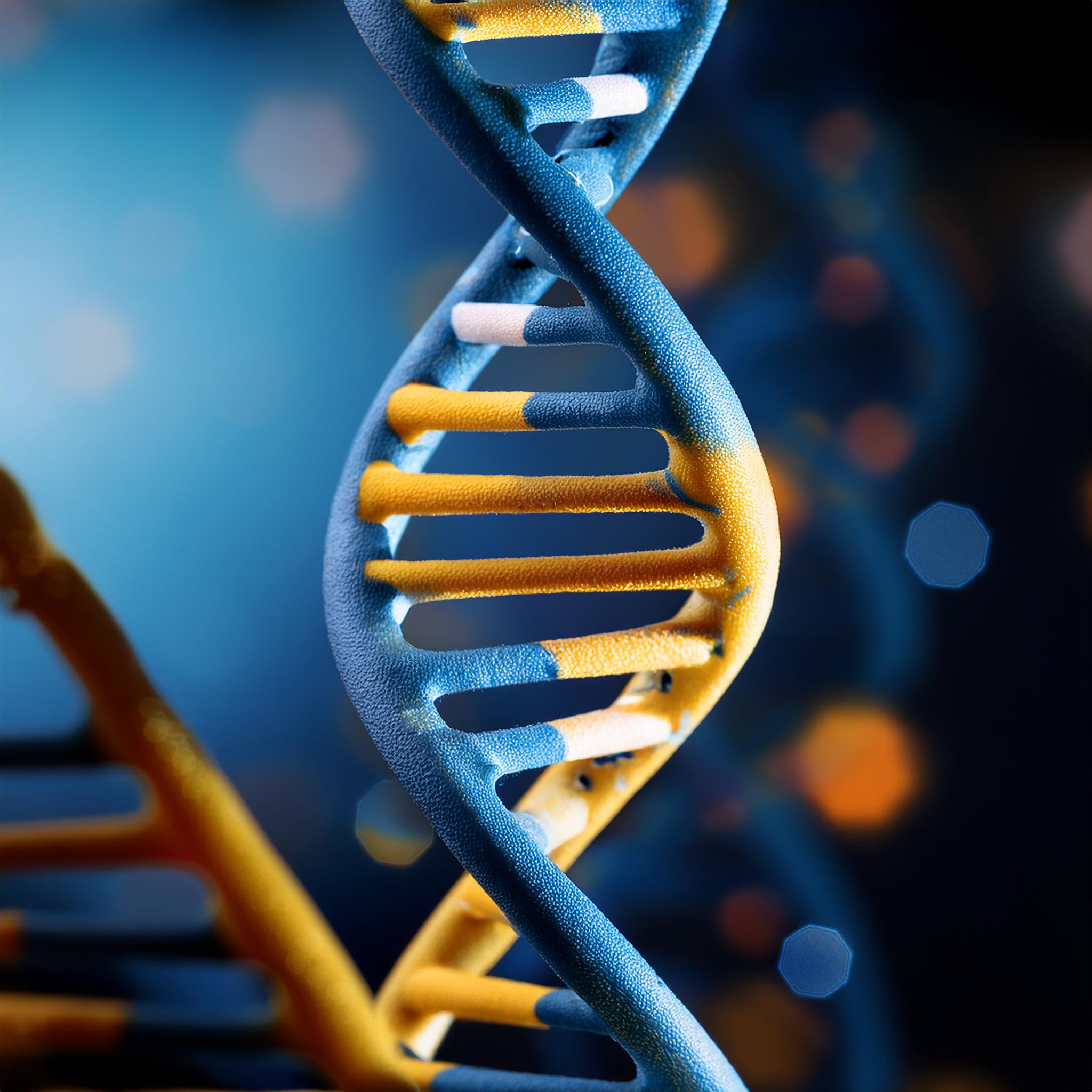
The continued growth of highly targeted biologics, like cell and gene treatments requires commercial productions at an agile pace and new strategies in place for quality pace requires a new path forward for biologics manufacturing. The demand represents good news: More and more people are getting life-improving and life-saving results from these innovative treatments.
The heart of AST’s ASEPTiCell is the flexible, robotic FCM, designed for commercial-level filling and closing of liquid pharmaceuticals. It offers in-nest processing for tubs and custom nest configurations for trayed formats. The FCM leverages simultaneous filling and nest handling with no wasted motion while maintaining First Air, making it an ideal solution for the development and production of the latest biopharmaceuticals.
Use Cases
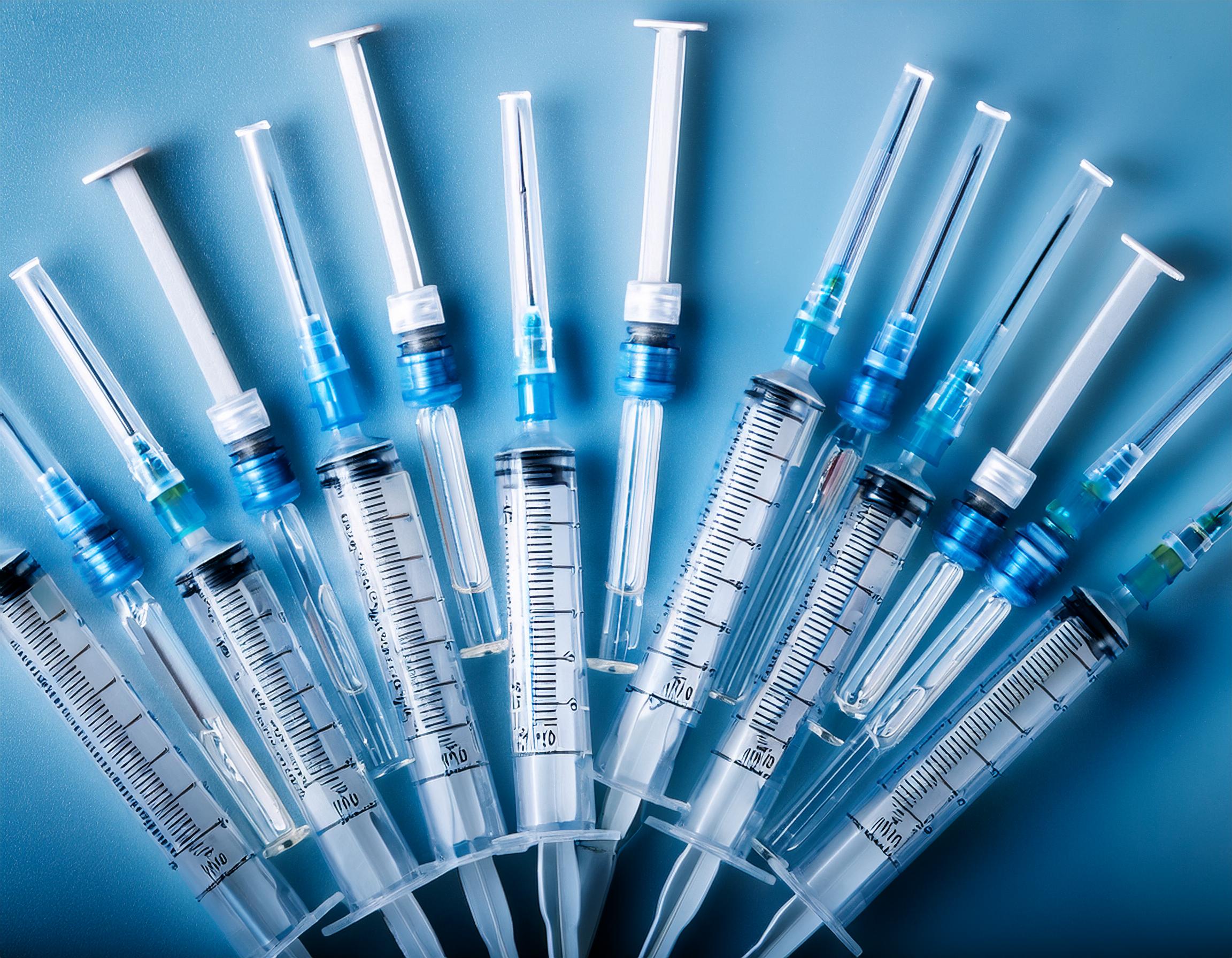
A leading contract manufacturing and outsourcing service provider partnered with AST on ASEPTiCell for a fully automated fill-finish production system.
Download the Case Study