4 Factors to Consider when Scaling Up
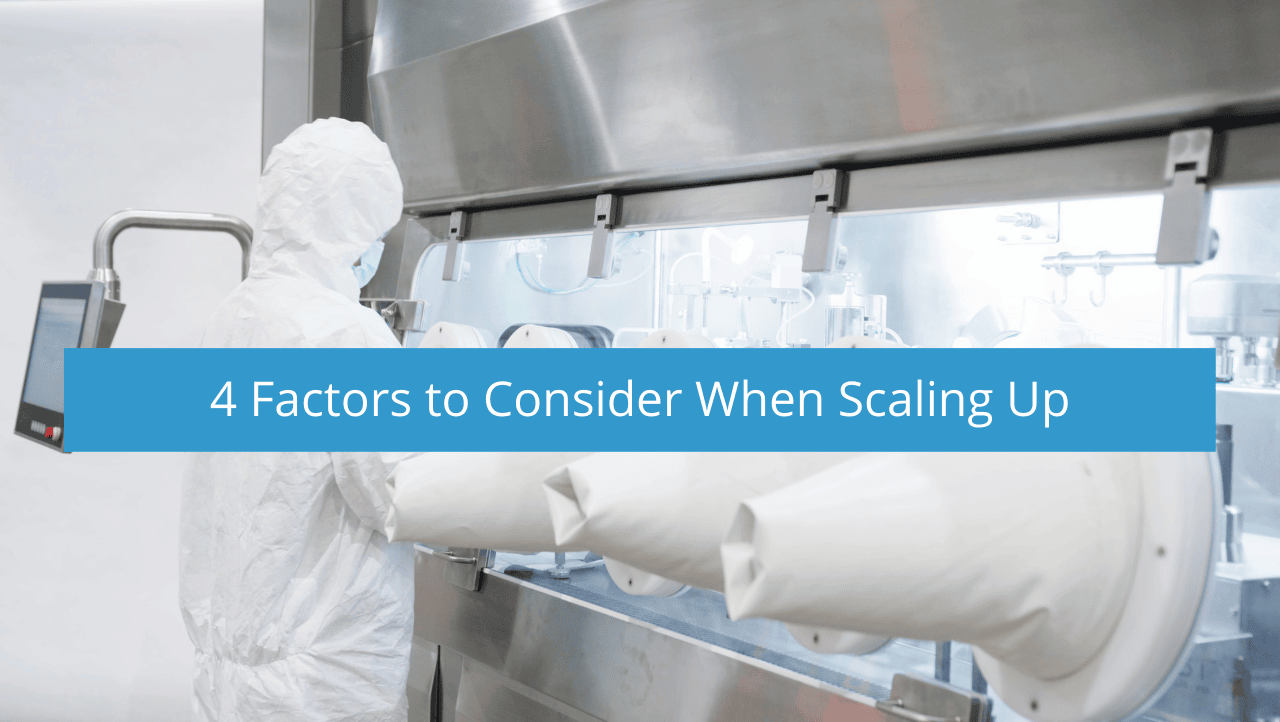
Moving forward to the next phases of clinical trials is an extremely exciting and hectic time. Understanding how scaling up affects your aseptic filling operations is essential. Here are 4 topics to consider that will help ensure that your drug product will be taken care of and be ready for production while increasing your ROI.
1. Technology Transfer/Established Technology
Scaling up is a continuous process, and your technology should be keeping up with you the entire way. There is no need to make things more complicated or add new aspects to an already stressful time.
Direct tech transfer between equipment eliminates a few issues. First, it eliminates the need for revalidation. If you have recipes on a lab-scale machine, you can easily transfer that recipe directly to a larger machine with minimal revalidation if key technologies, such as pumps or container closing, remain the same. A smaller, but still important issue is needing to learn something new when moving to larger scale aseptic filling machines. Having a familiar aspect of technology will help ease the transition and flatten the learning curve for operators.
2. Flexibility
Can you pivot or use your current machine(s) for more than your current project?
Looking for flexibility within aseptic filling operations will make it easy for you to scale up as your business grows. Itâs a built-in solution for you to expand your drug product processing capabilities as well as an antidote for market and drug process development uncertainty.
Giving yourself the ability to fill different types of containers and accommodate different processing needs quickly helps keep costs down significantly and makes your business more agile as market conditions inevitably change.
3. RTU vs. Bulk
When planning to scale up, weighing the costs and benefits of ready-to-use (RTU) vs. bulk containers will be essential to deciding what containers and aseptic filling machinery you will use. There are advantages and disadvantages to both, and it will be important to weigh the options together.
While bulk might seem more cost-effective up front – there are additional aspects to consider like safety, production, additional cleanroom space, utility costs, processes to validate, and sterilization that could account for extra costs that you wouldnât have to deal with for RTU.
4. Product Waste
Product waste is something that requires both a proactive strategy and a retrospective check to make sure that waste is kept to a minimum. Itâs the most tangible way to increase your ROI and can easily be overlooked if you arenât being careful.
Utilizing a 100% IPC system with zero-loss strategies that prevent containers from being over- or under-filled, along with optimized fluid paths, ultra-accurate pumps, and contamination control is the most effective way to ensure that your containers are being filled exactly as intended. To demonstrate accuracy and compliance, it is recommended to have full batch accountability and traceability in an electronic batch record (EBR).
These 4 factors for properly scaling up aseptic filling operations at your organization can ensure proper drug production while enhancing ROI. Contact our aseptic processing experts today and find out how we can help your organization.