By Steven Ng, CTO & VP of Customer Service
This past October, AST announced a groundbreaking collaboration with Germfree on a new fill-finish isolator. This exciting announcement was the result of just over a year of brainstorming, research, and development, as our team at AST set out to create an isolator solution that would meet and exceed our customers’ expectations and redefine aseptic fill-finish processing in an isolated environment.
As we are committed to doing at AST, our journey to designing a new isolator began by listening to our customers and pushing to find not just the best solution available, but the best solution imaginable. Our team started by asking what the ideal isolator barrier solution would look like. This question not only led us to consider the technical excellence of the isolator itself, but also common obstacles facing isolator fabrication, delivery, and servicing. We quickly determined that the right solution must involve both innovative engineering and rethinking conventional supply chain practices. We set the bar high, rolled up our sleeves, and got to work.
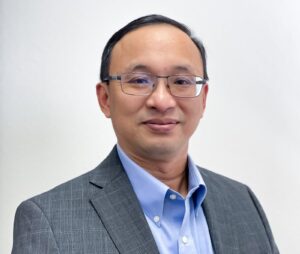
The status quo for fill-finish isolator manufacturing is well known within our industry. Lead time for manufacturing and delivery can average anywhere from 1-2 years. Common upkeep and standard maintenance–like changing out HEPA filters—often require two people, and long implementation times have become the industry norm. Current isolator design, while effective, often includes large, inflexible builds with overhang and non-automated, manual components backed by inordinately long servicing times. This forces many operations to make accommodations for these expected difficulties with regard to space and operational efficiency.
But what if this didn’t have to be the case? Could a more compact, flexible solution be built? Thus, our goal for the new isolator became clear: to create a more efficient, meticulously engineered isolator solution that was effective, simplified, user-friendly, and aesthetically engaging. What followed was an exciting process of creative collaboration. AST engineers conceptualized a new fill-finish isolator design, and in joining forces with Germfree—a global leader in isolator manufacturing—saw that design come to life. The result of that collaboration is a new class of isolator: a technically superior, cGMP-compliant product with improved efficiency and sterility assurance, all backed by a localized and responsive supply chain.
The AST Isolator design includes:
- Aesthetic, modern design with no gapping or incongruity in the frame, including efficiently placed tech housing, ducting, and motor drives
- Compact and flexible, able to fit in a room with ceilings as low as 10 feet
- Improved visibility and accessibility
- Optimized airflow systems
- Game-changing new VHP solution providing industry-leading bio-decontamination cycle times
- Aesthetic, ergonomic glove ports fortified by stainless steel, designed for easy glove installation with minimal risk of tearing
- Smart Design, including comprehensive sensor and instrument coverage, an Integrated PAO generator, and an innovative glove testing system
- Enhanced for operator experience and easy to clean
- State-of-the-art HMI with system-wide batch reporting and controls, including semi-automated filter replacement and air distribution membrane placement.
- American-made and American-backed; isolator manufacturing, delivery, and servicing that’s available in a fraction of the average lead time
In the coming months, the AST team will take an in-depth look at this new isolator solution, walking through each of its defining features and functions. Since our very first pioneering multi-format aseptic processing line for RTU containers, we’ve provided precisely engineered aseptic solutions rooted in American ingenuity. Stay tuned and feel free to contact our experts at AST as we explore the next stage of aseptic fill-finish innovation.