The following 2-part blog series has been adapted from AST’s VP of Sales and Marketing Josh Russell’s recent article in Cleanroom Technology.
As fill-finish automation continues to make exciting progress, the question of how best to implement automated solutions in an isolator setting continues to be raised, specifically as it relates to gloved vs. gloveless applications.
Broadly speaking, the benefits of aseptic processing within an isolator setting are clear. In many cases, it’s economically prudent over the life of an operation to run fill-finish processing in an isolator as opposed to lesser barrier settings. From a sterility and compliance standpoint, isolator technology is the obvious choice; regulatory standards, such as the latest Annex 1, reflect this reality. The drive towards greater sterility is a foundational and guiding principle in the pharmaceutical industry, and one trend that has remained consistent over the decades is that if there’s a path towards greater sterility assurance, the industry will follow it as quickly as technological advancements allow.
This motivation is what makes the current moment in isolator technology so intriguing. It’s well understood that whether through direct interventions or pre-handled equipment introduced into an aseptic setting, human beings are the single biggest threat to sterility in the fill-finish process. Any aspect of the fill-finish process or environment that can be successfully automated to design out interventions lessens the overall risk of loss in an operation and raises product quality standards. And while in a perfect world, automation would work 100 percent of the time, imperfect functions and unanticipated events will always exist and require that operator interventions, both planned and unplanned, be forecasted.
And if practical, real-world scenarios are taken into account with the wide array of circumstances and obstacles possible, perhaps it’s not an either/or choice. What if the path forward isn’t a matter of “gloveless” per se, but rather a matter of less gloves?
Considerations for Gloved Isolators
Gloved isolators are designed to run without human interaction, but even the best machines will require intervention at some point. The logic of a gloved isolator design accounts for planned interventions like changes in the environmental monitoring system or introducing sterile equipment into the fill line. Glove ports are also useful in corrective actions and certain non-qualified machine emergencies. When a batch worth millions of dollars per vial stops due to an easily fixable problem, for example, you don’t want to be George Costanza from Seinfeld standing on the outside of the vending machine, yelling at the candy bar to “jump!” when you are entirely unable to do anything about it. These types of inevitable scenarios illustrate both the good sense of a gloved isolator for certain operations and an area where gloveless isolators have substantial room to further demonstrate proof of concept.
For a gloved isolator, having comfortable and easy ergonomics is key. Making your operators’ jobs easier by having procedures in place to dictate when an intervention is allowed and what types of interventions are permittable is essential. A poorly designed glove port offers all the dexterity of a high school mascot costume, and that sort of inconvenience hampers operational productivity at best and, at worst, causes riskier interventions that require sterility protocols to be repeated. Having the ability to intervene or work ergonomically and aseptically—without introducing contamination or violating first air—should be a high priority on par with efficiency.
That being said the requirements of gloved isolators are well understood. Any iteration of a gloved isolator comes with substantial cGMP protocols, as an ingress into isolator space can represent a potential pathway for contamination. Annex 1 specifies that inspection and maintenance of gloves and glove ports should be conducted at frequent intervals. In practical operational terms, this includes a thorough preventative maintenance program, routine performance of glove integrity tests, visual inspection of gloved areas with every use, and frequent glove replacement that makes sense within the scope of the operation. A successful QMS approach depends on the accuracy of these procedures and the diligence of the operator. Many of the recent advancements, whether it be material use or quality control measures like glove testing technology, have only improved sterility and validation protocols.
A Matter of What Works
Gloveless solutions have been a focal point of the latest developments in isolator technology as the industry looks for viable, accessible advancements towards greater sterility assurance and product quality. The crux of the discussion is what a gloveless solution actually can and cannot accomplish in an operational setting. A gloveless isolator may reduce human interventions, but can it eliminate them completely? They may reduce risk in some areas, but if we eliminated every glove port from an isolator, would that equate to the low-risk solution some tout it to be? The truth is that no matter the automation, failure and consequently, unplanned interventions are always a possibility.
The choice then centers on the tension between what’s possible and what’s practical, and an accurate assessment of how we get the most out of various automated solutions. In the design of the new AST isolator, AST’s goal was to marry the best of automation with practical, sensible operational redundancies. In our view, a well-placed, well-constructed glove port working in concert with smart, highly flexible automation is the key to reducing risk and safeguarding product integrity. The best automation removes human risk without removing humans from what they do best: problem-solving, strategizing, and adapting.
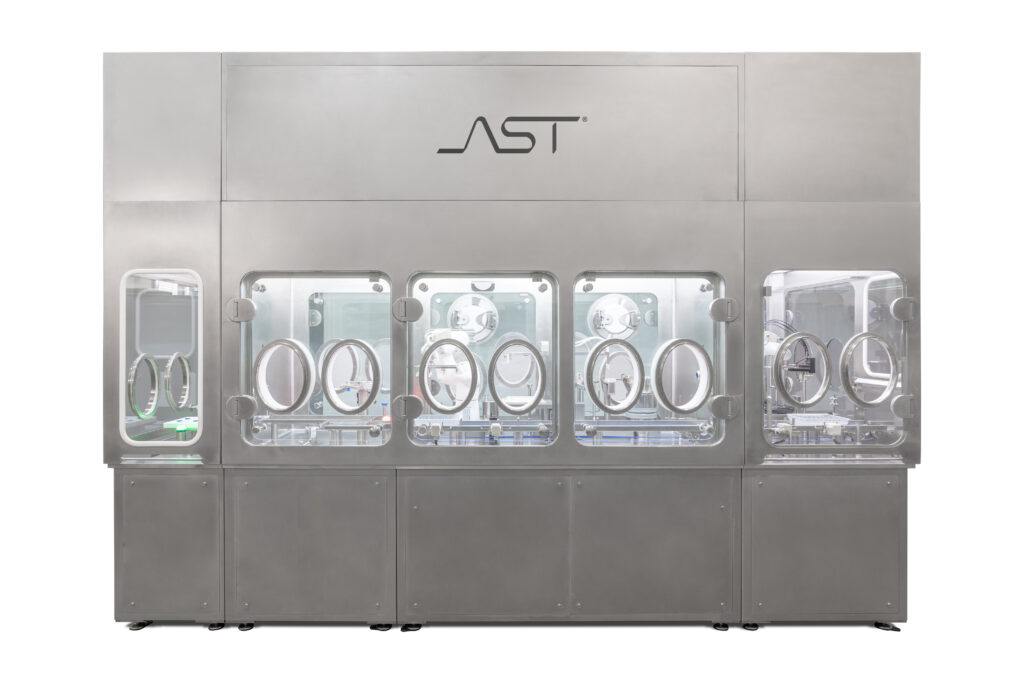
Stay tuned for Part Two next week as we delve into the look regulatory emphasis on automation and why gloved redundancies are necessary for a comprehensive quality control strategy. Learn how AST can provide your organization with the next generation of high-quality isolator technology – contact our experts today.