Recent regulatory updates, including the revised Annex 1, have put isolator technology in the spotlight as the recommended solution for the filling of sterile parenteral products. The pharmaceutical industry has shifted strongly towards the use of appropriate barrier technologies and is looking for solutions that both excel in protecting high-value liquid pharmaceuticals and offer the latest in innovation and time-to-market advancements.
The Atmos™ isolator, designed in collaboration with Germfree, is the latest in turnkey aseptic processing technology from AST. Leveraging the same innovative approach from our fill-finish lines, this isolator solution features next-generation barrier technology built to meet the full scope of fill-finish processing. When AST set out to design a fully integrated isolator, we had one goal in mind:
Create a solution that sets the standard in efficacy, efficiency, and user experience.
Our starting point was common, everyday obstacles faced by aseptic fill-finish professionals. We aimed to innovate past many of the pain points encountered across the industry in a way that directly streamlined and simplified effective isolator protocols. Our team asked: what could a solution that met both the most stringent regulatory standards for air handling and the ever-growing operational demands of accelerated drug development look like?
The result is a robust Grade A environmental solution outfitted with intuitive design, ergonomic advancements, and groundbreaking time-to-market improvements, all constructed with the highest quality materials available.
AST Atmos features:
- Exclusively integrates with our fill-finish systems for a 100 % turnkey AST solution
- Compact, flexible design
- State-of-the-art automation and operator-friendly features
- Industry-leading decontamination cycle times
- Backed by a localized model for support and service
- Built for Annex 1 and beyond
Industry-Leading Decontamination: 1 hr. Start-to-Finish Cycle Times, Including Aeration
With the cutting-edge use of low-volume, 7 percent Vapor Phase Hydrogen Peroxide, the AST Atmos sets a new benchmark in sterility assurance and contamination control for the pharmaceutical industry.
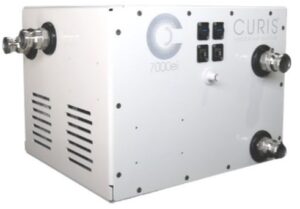
With the cutting-edge use of low-volume, 7 percent Vapor Phase Hydrogen Peroxide, the AST Atmos sets a new benchmark in sterility assurance and contamination control for the pharmaceutical industry.
By introducing low-concentration Vapor Phase Hydrogen Peroxide, AST’s isolator solution achieves greater than a 6-log sporicidal reduction and Grade A / ISO 14644 class 5 operations with CURIS System’s patented Pulse™ technology, which maintains an optimal, non-hazardous concentration of VPHP throughout the decontamination process. This equates to an aseptic processing solution with less downtime, repeatable efficacy, and a new level of sustainability.
Why Now is the Time for Isolated Fill-Finish Production
The advancements in barrier technology in recent years have been significant, particularly as it pertains to air handling, biodecontamination, automation, and cross-system integration. As the life sciences industry has increasingly moved towards isolator-based operations, regulatory emphasis has followed. Annex 1, as an example, now regards the use of barrier technology as the standard mode of operation for the filling of sterile liquid pharmaceuticals and leveraged its technological advantages for an increased emphasis on First Air and unidirectional airflow. Combined with the regulation’s emphasis on appropriate and rapid technologies, automation, and an active, continually improved Contamination Control Strategy, it’s clear that utilizing the right tools and advancements during the fill-finish process leads to higher, and now expected, standards of quality and safety.
In addition to the time-saving solutions, isolated fill-finish operations have a demonstrable cost of ownership advantage over a traditional setup. When compared to the cost of production inside a cleanroom or a lesser barrier option, the net cost savings provided by isolators are substantial. Energy use, HVAC infrastructure, the annual cost of operation, contamination risk, growing requirements, and the overall footprint of the operation are all areas where isolator technology specifically offers clear economic benefits to a project.
As a one-stop source of supply, service, and strategy, AST’s turnkey approach addresses the full scope of an operation, from project planning and implementation to production optimization and aftermarket support. Finding a single partner for the design of an isolator, fill finish system, and the necessary technological and data solutions equip pharmaceutical manufacturers with a new dimension of responsiveness and agility.
With the addition of the Atmos Isolator, AST is the exclusive full-service provider of American-made fill-finish solutions. Reach out to one of our team members today for an in-depth walk-through of the Atmos Isolator.