PRODUCTS
Key Technologies
AST’s aseptic processing solutions are outfitted with the latest in intuitive cGMP technology designed to optimize the fill-finish process for the highest standards of quality and regulatory compliance.
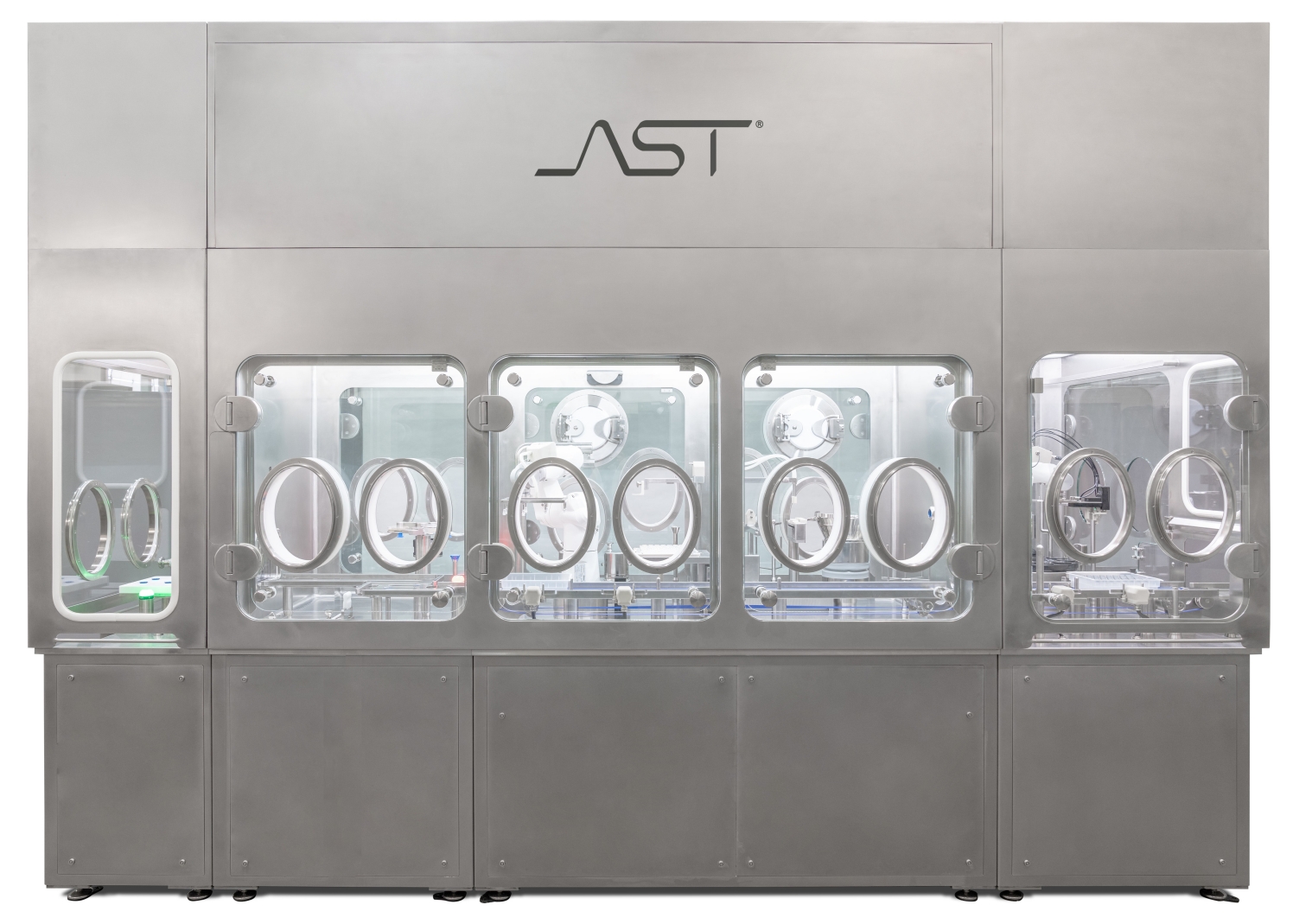
Pioneering Flexibility in RTU Processing
AST has led the flexible aseptic manufacturing movement since the design and launch of our first ASEPTICELL, which was the industry’s first multi-format system designed to process ready-to-use nested vials, cartridges, and syringes. Now an industry standard, multi-modal pharmaceutical manufacturing stakeholders are looking for ways to grow pipeline agility through proven cGMP technology. AST’s integrated lines offer fill-finish processing for the full range of commercial and custom RTU formats and product applications.
The RTU Advantage:
- Enhanced sterility assurance
- Faster qualification and process validation
- Significant savings on equipment, facility, & operations
- Increased speed to market.
- Flexible closing and sealing options for syringes, cartridges, and vials.
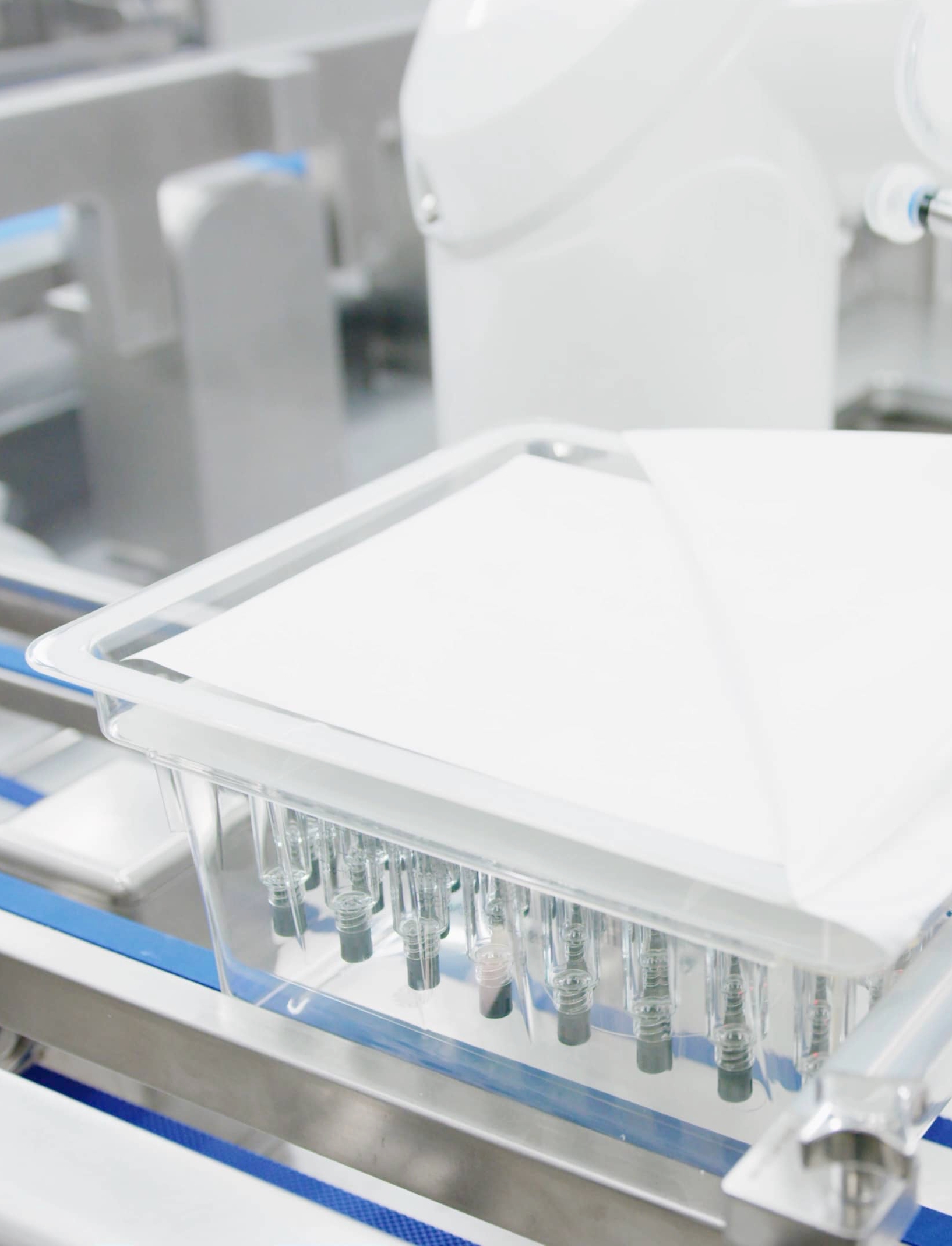
Formats | AST systems are compatible with:
- Ompi EZ-fill™
- Schott adaptiQ™
- BD Hypak™
- West CZ™ (trayed and nested formats)
- SiO2™
- And many more, including custom formats
Technology Highlights
In-Process Weight Checks
Non-destructive in-process weight checks verify that every container is filled to specification and ensure that product yield is maximized. Features of this innovative system include:
- Batch start-up mode that allows priming the fluid path without wasting any product by filling the first few containers on an analytical scale.
- Batch end mode that places the last few containers on an analytical scale to ensure that every possible drop of product is used.
- Pump calibration performed using feedback gained during statistical IPC checks
- Recipe-programmable weight checks to allow for statistical or 100% IPC
Augmented IPC is an available option that adds new capability to In-process weigh checks. AST’s approach, Augmented IPC, leverages a flow-based system programmed to work in concert with an analytical balance to ensure the quality threshold of 100 percent IPC is met while a machine remains in a high-speed, statistical IPC mode.
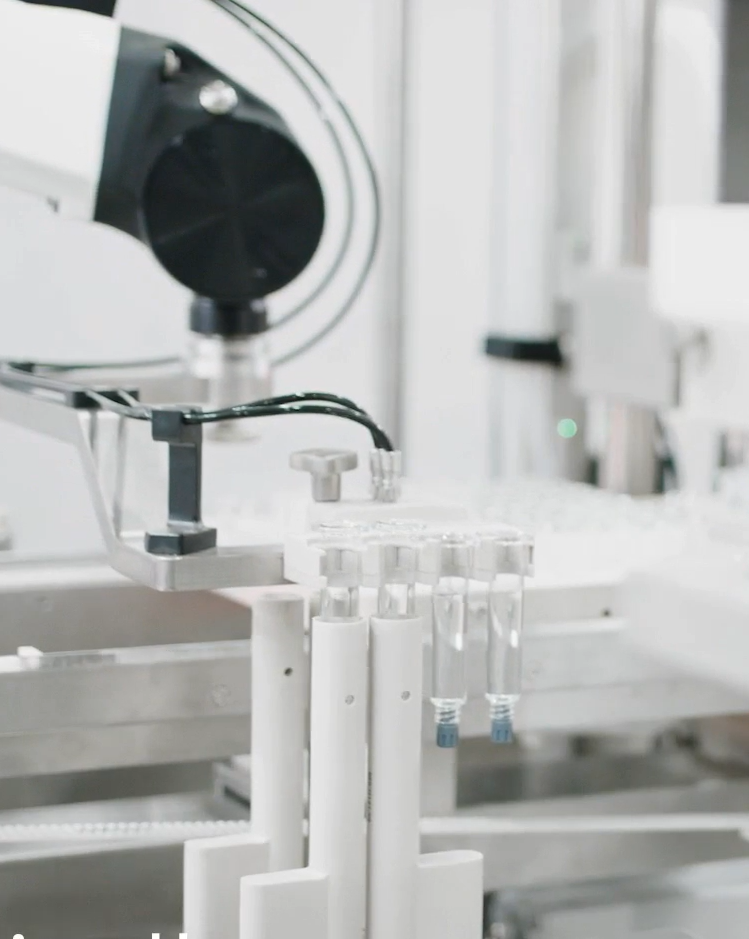
Environmental Monitoring
Environmental monitoring is a critical consideration when designing and implementing your aseptic operation. With the growing development of highly targeted liquid pharmaceuticals, there are increased expectations around quality as reflected in regulatory emphases like the revised Annex 1. AST provides expertise and guidance for the proper EM placement and strategy for your environmental monitoring program.
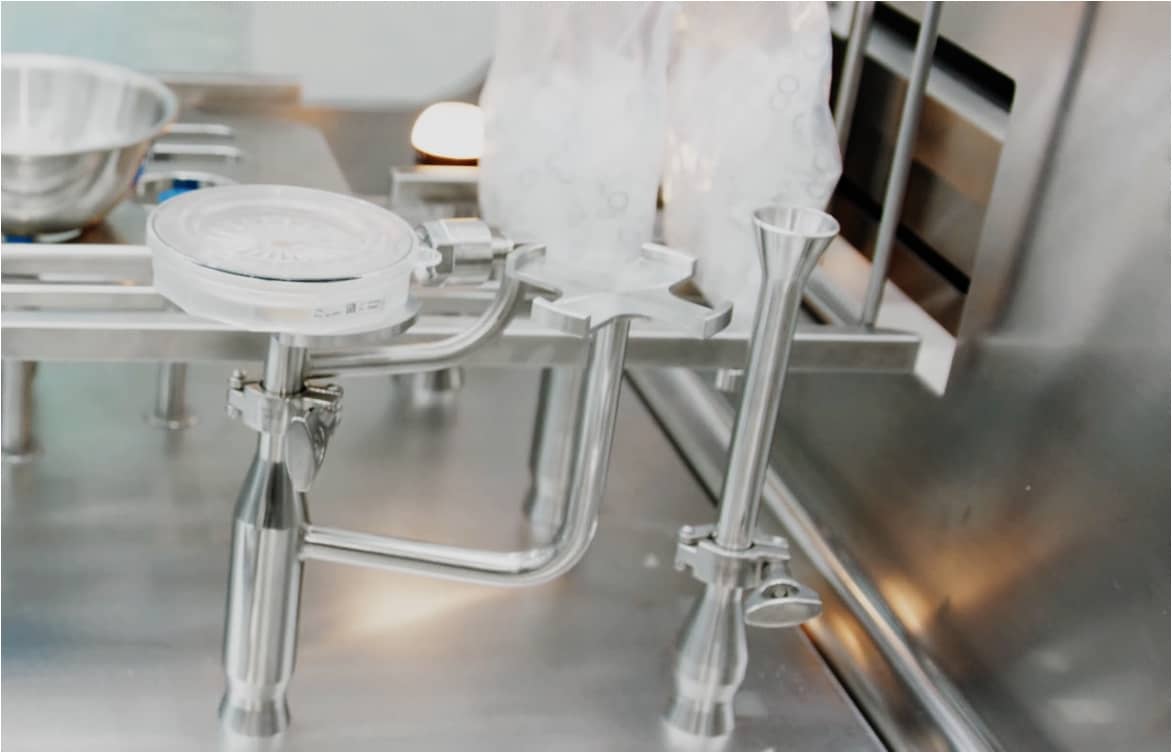
Total particulate, active viable, and passive viable environmental monitoring stations placed strategically throughout processing stations ensure ideal environmental conditions and provide a record of environmental data to your batch record system.
AutoEM – AST’s automatic plate changer for active and passive viable monitoring
Automatic environmental monitoring is available to automate and de-risk environmental monitoring process interventions. The EM plate-changing tool utilizes pre-sterilized settling plates that are aseptically introduced into the fill line and loaded into an inline cassette dispenser. Plate changes are automated through the HMI, saving process time on typically manual, ergonomically unfriendly gloved interventions.
AutoEM Highlights Include:
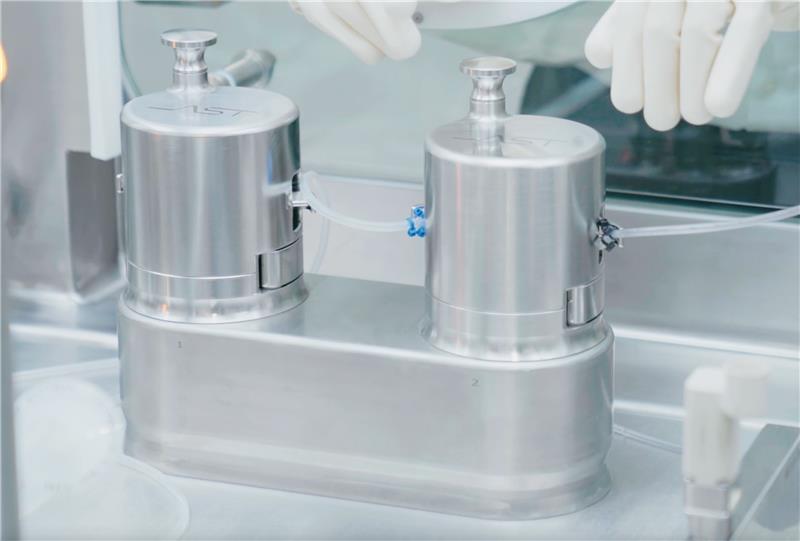
AST Pump Technology: Peristaltic and RPP
The AST peristaltic pump is a gentle peristaltic pump designed for dispensing shear-sensitive products. AST’s approach uses pre-sterilized single-use fluid paths that can easily be installed in the pump in an isolated setting through the glove port, ensuring sterility and that the pump remains non-product contacting. Outfitted with a safety sensor, the pump lets the user know if the door is ajar and the fluid path is not secure. The pump is stationarily built into the fill area to allow easy cleaning, eliminating hard-to-reach spaces and the need for pump removal. AST peristaltic pumps are designed to allow operators to ergonomically install fluid paths through isolator glove ports using one or two hands depending on what is most comfortable for the operator.
AST’s rotary piston pump assembly is a compact solution for highly viscous products available in a full range of pump sizes and product-specific coating options. The pump is constructed of high-quality stainless steel and autoclavable.
AST pumps come installed on the FCM and can be configured to multiple fill lines or a combination pump approach utilizing both rotary piston and peristaltic assemblies. Pump technology is servo-driven for precision and completely integrated into the system HMI for ease of operation, process traceability, and batch recording.
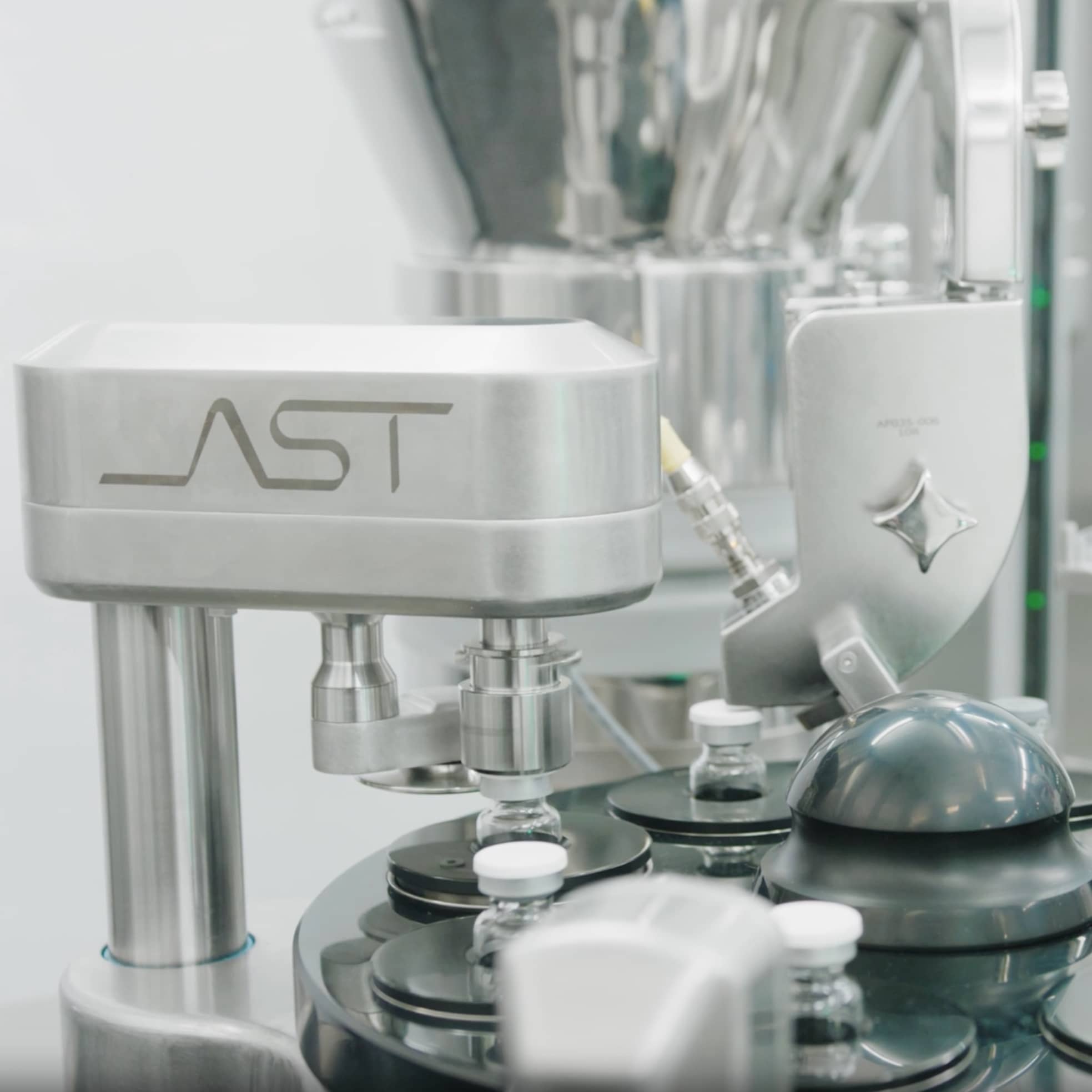
Vial Sealing
Fully automated, cGMP compliant vial sealing is available across AST's entire line of fill-finish equipment. Features include:
- Low particle crimping using a gentle and precise free-spinning disc design. This approach forms a pharmaceutically aesthetic seal and provides scratch-free capping for polymer vials.
- Seal force monitoring to ensure a consistent, pharmaceutical-grade seal.
- Complete reject automation, including missing cap and raised stopper detection, and container removal.
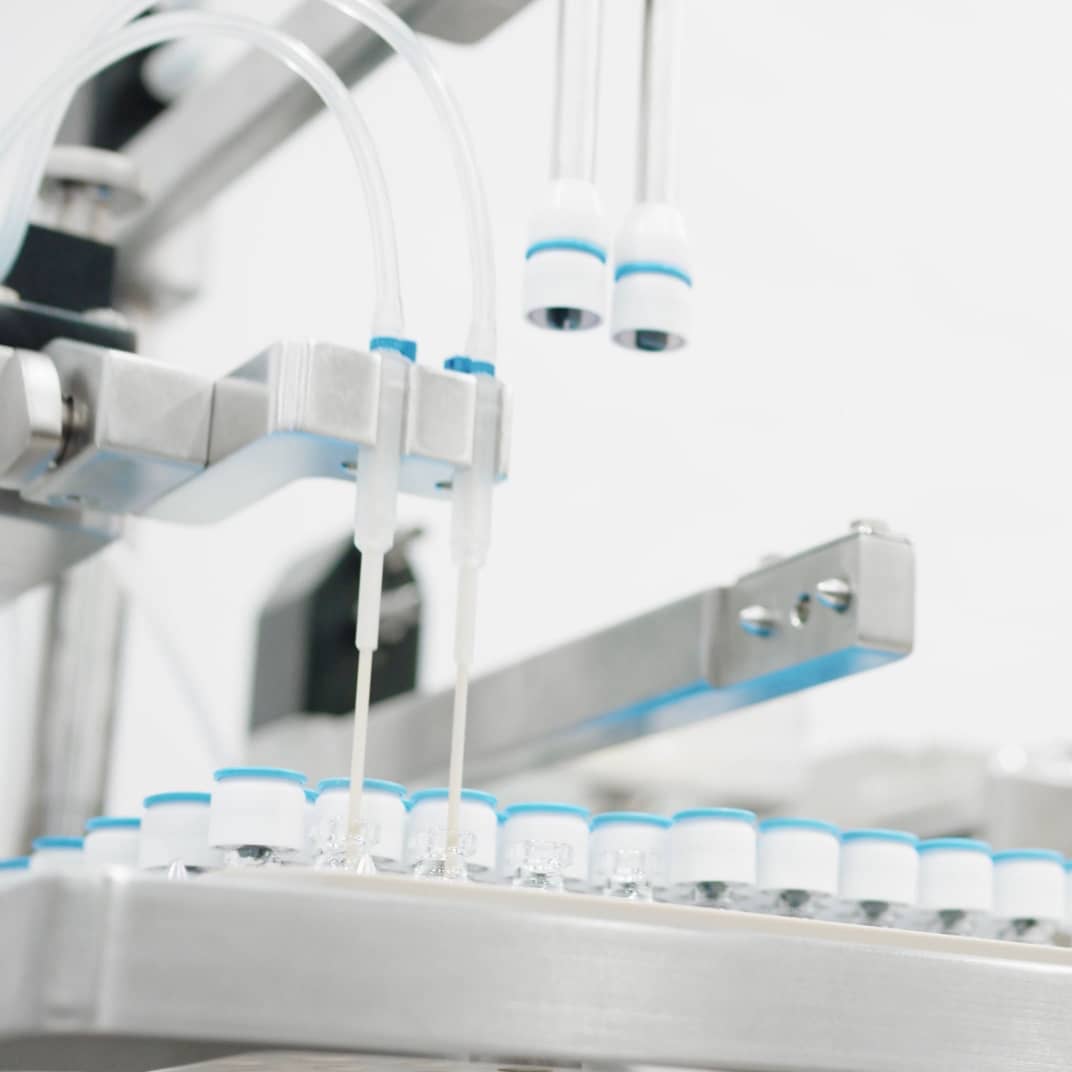
Press-Fit Cap Application
In addition to crimp capping in the Vial Sealing Module, press-fit cap application is available within the Fill / Close Module. This includes:
- Measurement of applied force to confirm proper seating force.
- Measurement of stopper compression distance to ensure seal integrity.
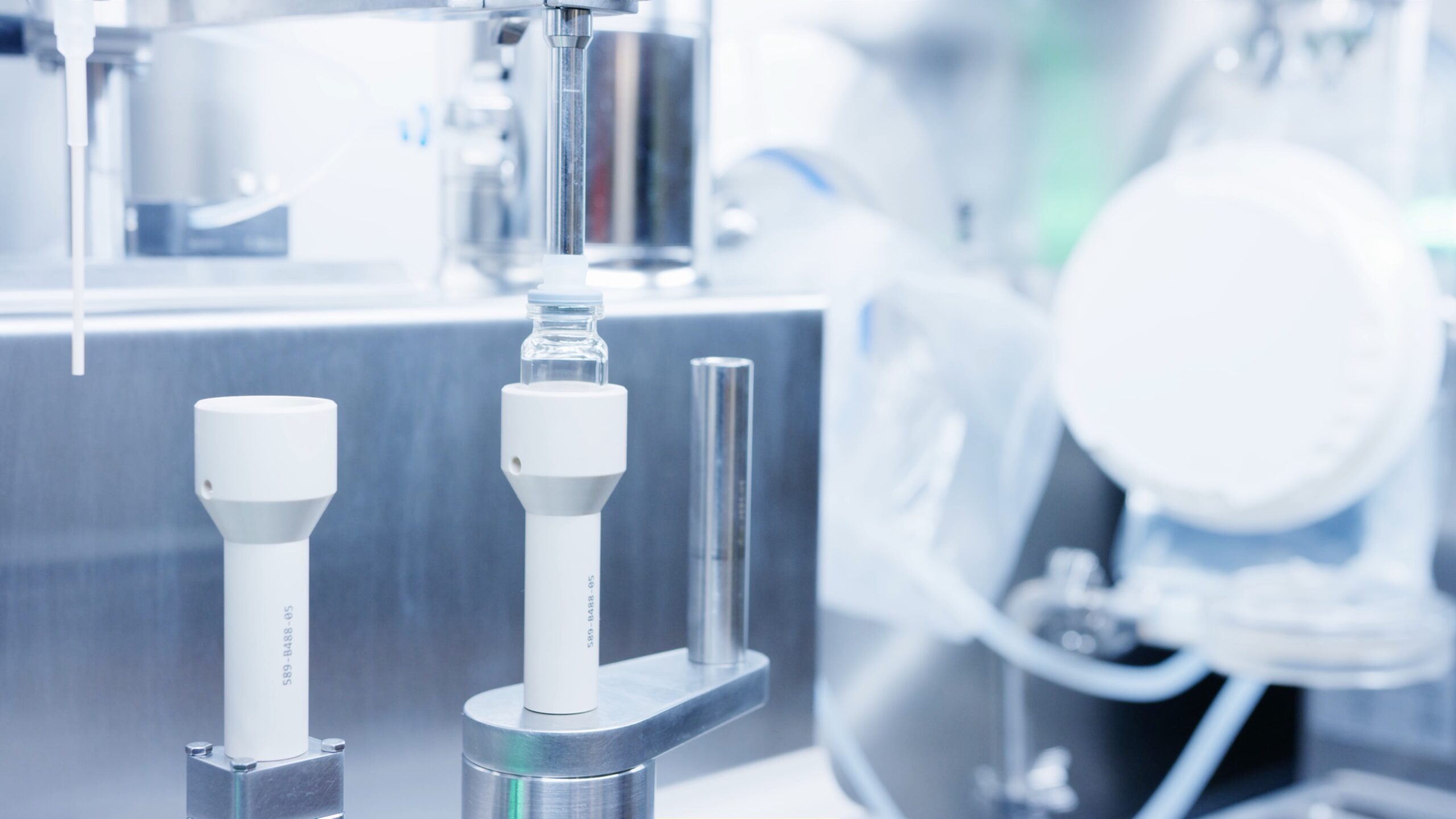
Gas Overlay
For sensitive products and materials, a sterile gas overlay system can be provided for purging before, during, and after fill. This system is optimized with single use gas-contacting components that are disposed of downstream to ensure sterility, and an optional coaxial needle to inject the purging gas is available.
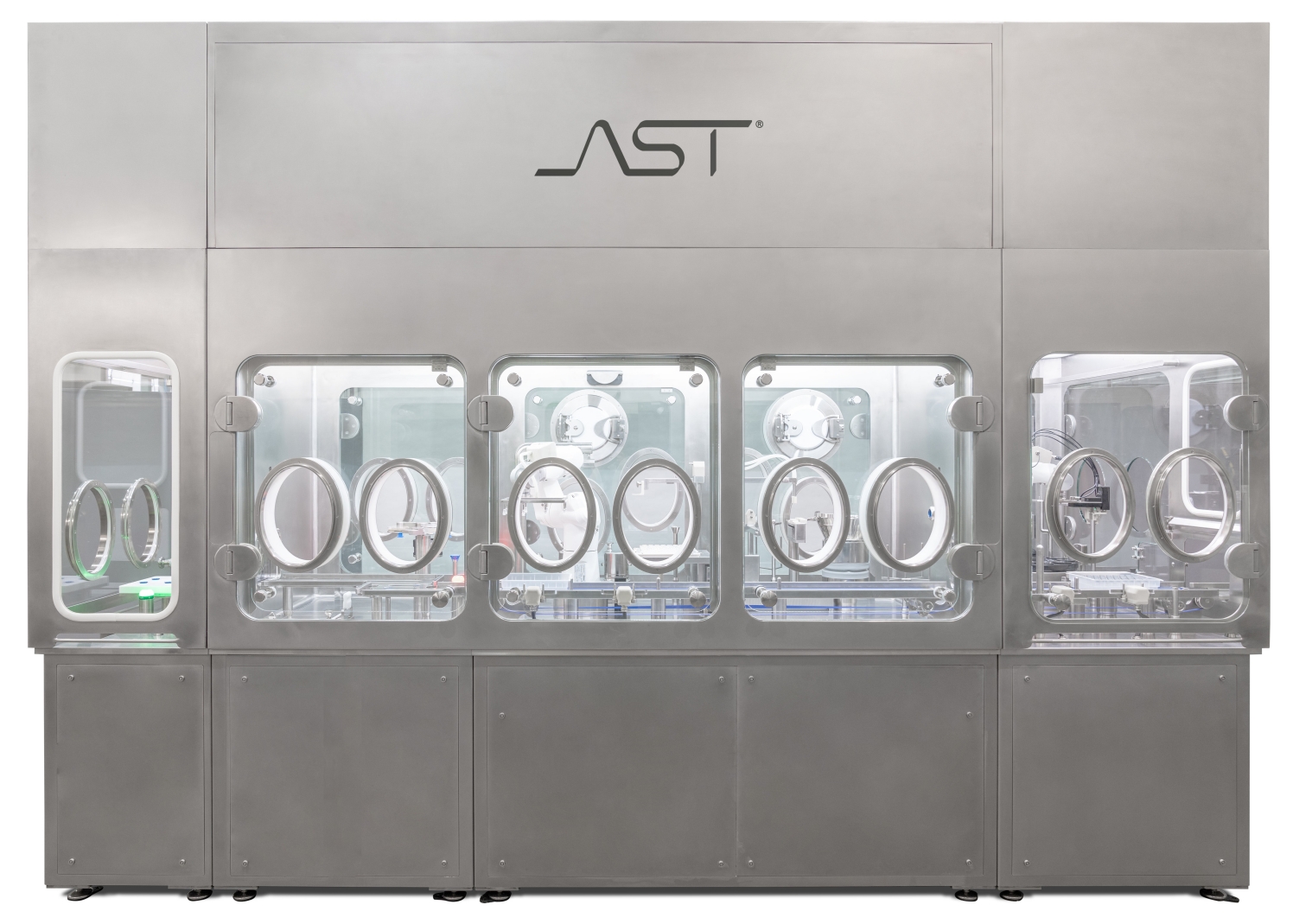
AtmosTMIsolator technology
A premier, cGMP-compliant product with improved efficiency, sterility assurance, and a state-of-the-art decontamination solution that provides industry-leading bio-decontamination cycle times. The only fill-finish isolator to be fully American-made, the product is supported by a responsive and localized supply chain for minimal downtime, and features full integration of the HMI (ASTView), FAT and environmental monitoring.
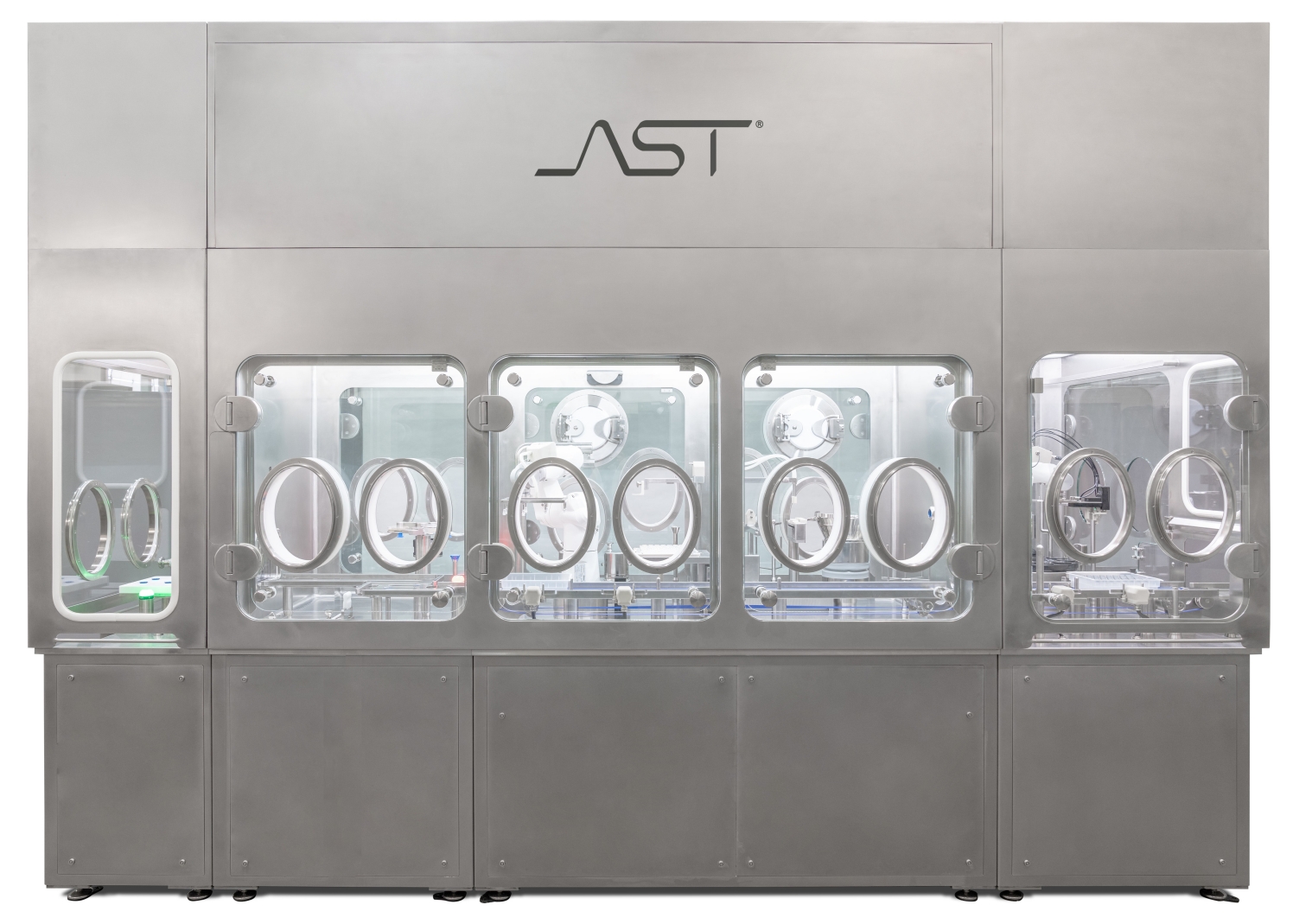
Human Machine Interface (HMI)
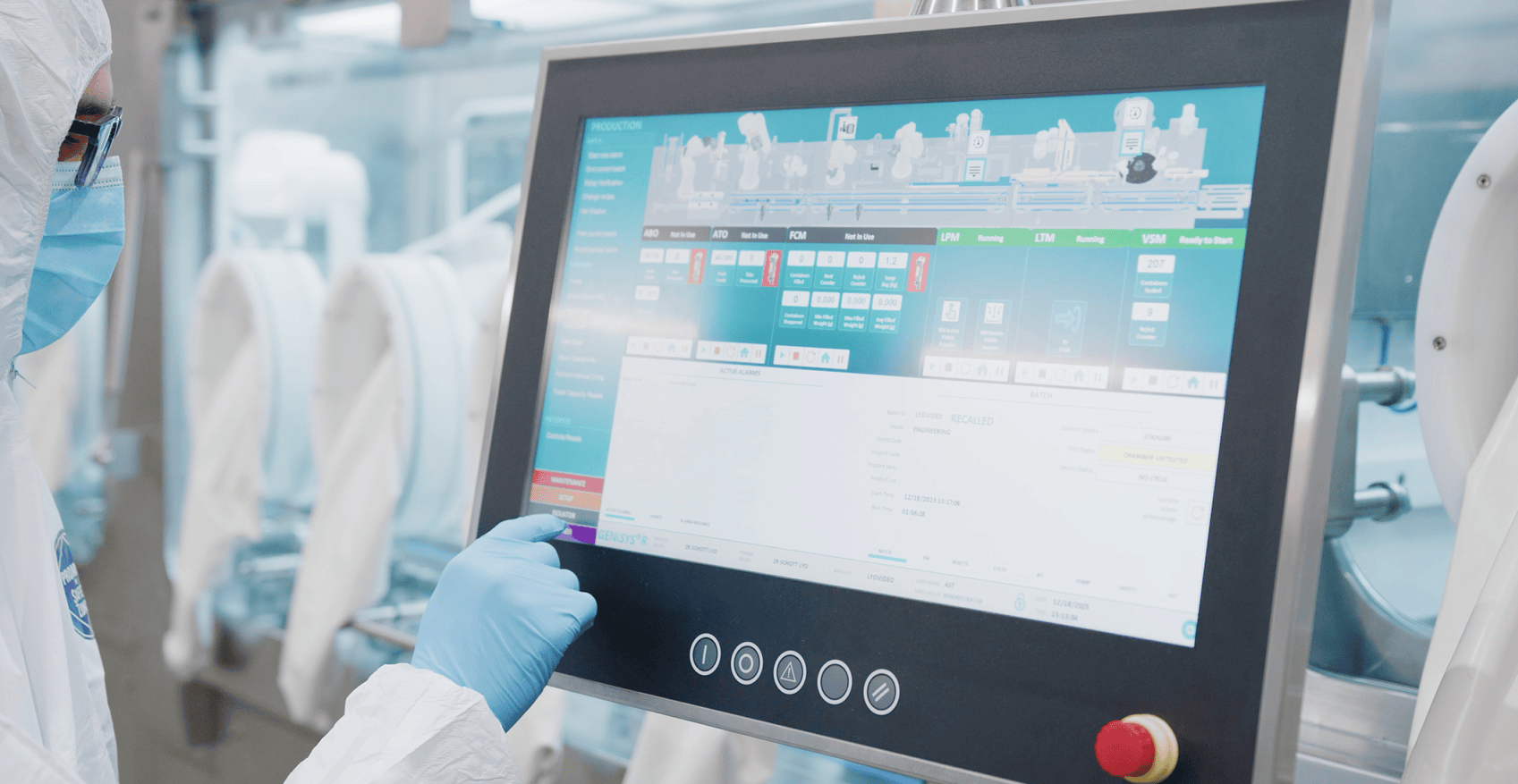
ASTView® is an intuitive program that fully integrates with AST’s aseptic fill-finish systems and isolator technology. Utilizing a user-friendly interface with a high-resolution color touchscreen, ASTView offers complete access to critical machine functions and in-process parameter data. Other features include:
- Fully exportable data in PDF formats
- Remote monitoring through Thin Client app available for smartphones, tablets, and laptops.
- Interface with optional EBR system.
Electronic Batch Record (EBR)
The ASTView EBR system offers operational traceability and simplifies batch recording and data integrity protocols by creating a batch report that is ready for 21 CFR Part 11 compliance, streamlining the regulatory and tech transfer processes.
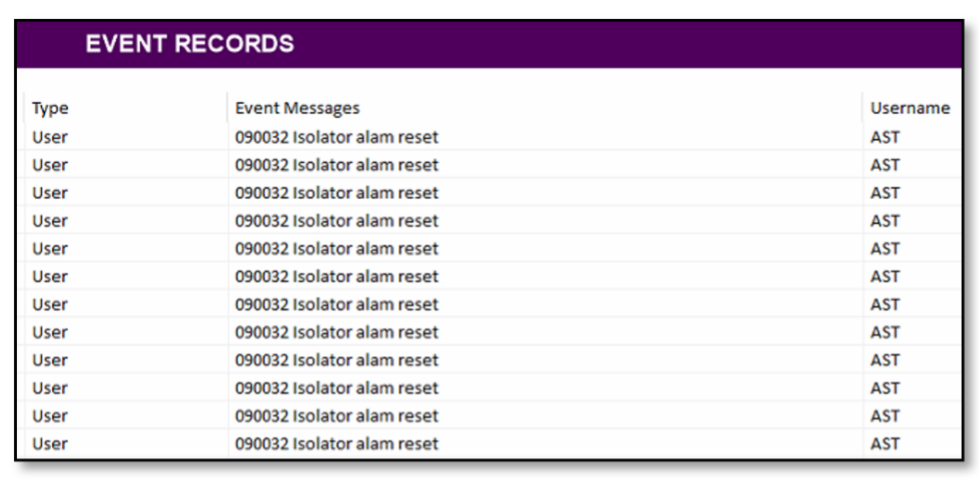
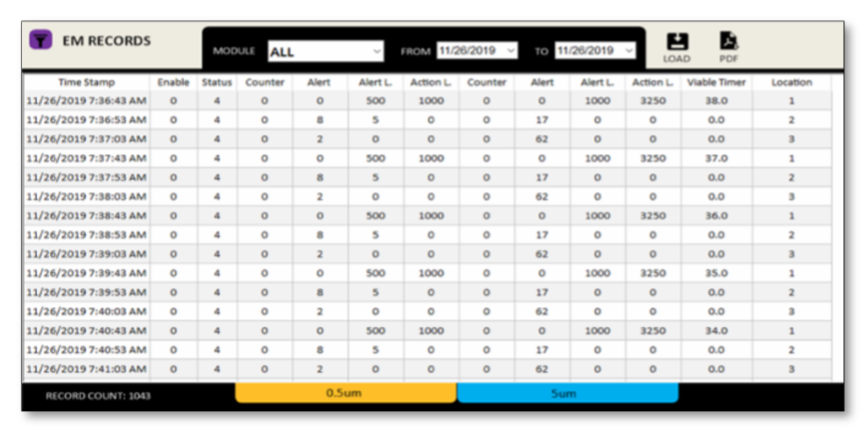
Technology Highlights
Change Parts
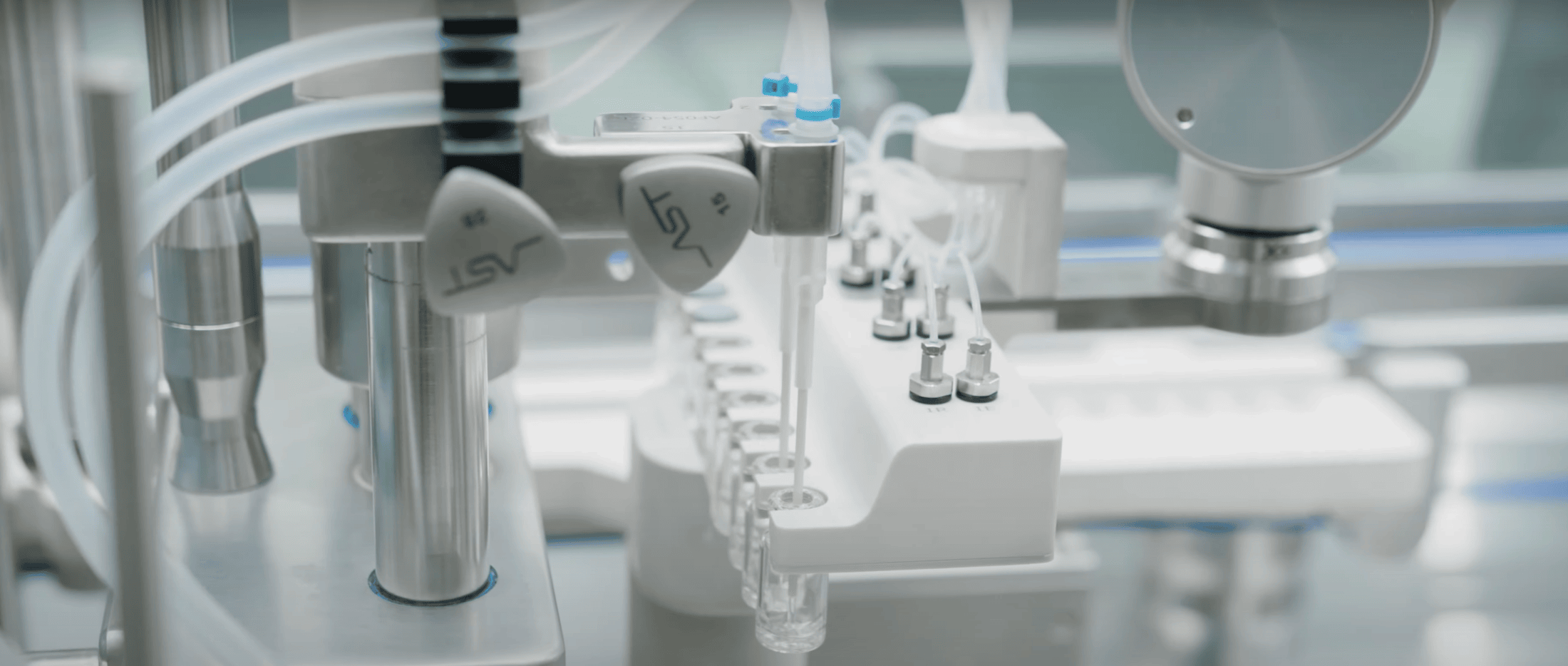
AST’s fill-finish systems are designed with minimal, as-needed change parts that are completely recipe-driven, autoclavable, and materially compatible with closed barrier sterilization measures. With ultimate flexibility in mind, a trained operator can complete installation on our largest system in 15 minutes or less.
A full range of recipe parameters can be loaded into the HMI and executed with minimal changeover time. Additional change parts can be ordered per module and replacement/maintenance will be provided by AST’s Customer Care Team.
AST change part features include:
- Parts can be sterilized easily and effectively, compatible with measures such as autoclaving
- Compatible with aseptic decontamination protocols such as vaporized hydrogen peroxide (VPHP)
- Parts that are replaceable and backed by a stocked, responsive aftermarket supply partner
- Designed to be “mistake-proof” and only able to be installed correctly, protecting the machine equipment and supporting operational uptime